Kluczowe zalety zarządzania lepkością w liniach rozlewniczych do produktów płynnych:
- Precyzyjne i wydajne operacje linii pakującej - znaczące oszczędności w kosztach materiałów
- Bezproblemowa zmiana produktu: sprawność w radzeniu sobie z różnymi i nowymi wariantami produktów oraz ich pochodzeniem
- Zgodność z przepisami
- Optymalizacja systemów CIP
Wprowadzenie
Opakowania płynne, płynne ze stałymi kawałkami i produkty podobne do żelu składają się z materiałów opakowaniowych i maszyn pakujących, takich jak linie napełniające. Obejmuje sztywne formaty opakowań, takie jak butelki i pojemniki, oraz elastyczne formaty opakowań, takie jak folie, woreczki stojące, tubki do wyciskania, kartony i torebki na pudełku. W wielu branżach procesy pakowania są zautomatyzowane za pomocą linii rozlewniczych.
Obszary zastosowań opakowań płynnych obejmują wiele gałęzi przemysłu - spożywczego i napojów, kosmetycznego, artykułów gospodarstwa domowego, chemicznego, leków, produktów FMCG. Oto kilka przykładów według branży:
- Żywność i napoje: sosy, produkty mleczne, soki, napoje gazowane, zupy, kawa / herbata, jogurt, mleko, lody, desery żelatynowe, miód, galaretka, syropy, żywność aseptyczna, masło, ghee, piwo itp.
- Kosmetyki: kremy, balsamy, szampony, olejki do twarzy, włosów, filtry przeciwsłoneczne
- Leki: syropy, krople, maści
- FMCG: Pasty do zębów, środki odkażające, płyny do mycia rąk, płyny do mycia naczyń, detergenty w płynie
- Chemikalia: Przemysł, uzdatnianie wody, kleje, górnictwo, katalizatory, laboratoria i inne zastosowania.
Mechanizmy napełniania / pakowania
Jednym z kluczy do udanej linii do pakowania płynów jest wydajność. Aby zoptymalizować wydajność linii pakującej, należy wziąć pod uwagę wiele czynników. Obejmuje lepkość cieczy, charakterystykę produktu, specyficzne wyzwania związane z produktem, łatwość czyszczenia, dokładność, łatwość elastyczności i przezbrajania oraz korzystanie z niezawodnego dostawcy maszyny.
Wszystkie płyny płyną inaczej. Zrozumienie tego jest niezwykle ważne podczas projektowania maszyny do napełniania. Lepkość to właściwość, która daje wgląd w zachowanie się cieczy. Dlatego ważne jest, aby zwracać uwagę na lepkość produktu, z którym się kontaktujesz. Metody napełniania różnią się kosztem, dokładnością, szybkością i higieną. Nie wszystkie metody są odpowiednie dla wszystkich płynów, gdyż napoje wymagają szczególnej higieny, drogie kosmetyki wymagają szczególnej precyzji, a olej silnikowy ma inną charakterystykę płynięcia niż np. Woda mineralna. Sypki produkt, taki jak woda o niskiej lepkości, będzie dobrze przepływał przez wypełniacz grawitacyjny. Dzieje się tak, ponieważ ten typ maszyny opiera się na sile grawitacji, aby przepchnąć produkt.
Niektóre produkty o wyższej lepkości będą wymagały pomocy przy umieszczaniu ich w opakowaniu. Balsamy i inne płyny o wysokiej lepkości dobrze współpracują z wypełniaczami tłoków i pompami. Wypełniacze tłokowe mają wszechstronną zdolność do obsługi płynów, od produktów napowietrzonych po polewy i sosy. Wypełniacze do pomp dobrze współpracują z płynami o każdej lepkości i oferują różnorodność, jeśli chodzi o wybraną pompę. Wypełniacze pomp mogą wykorzystywać progresywne pompy wnękowe, pompy zębate, pompy oleju i różne zawory i armaturę, aby spełnić potrzeby projektu.
Co sprawia, że automatyzacja i kontrola lepkości są tak ważne w budowaniu wydajnej linii do pakowania produktów płynnych?
Jednym z pierwszych aspektów linii pakującej, który firma musi wziąć pod uwagę, jest lepkość cieczy przechodzącej przez procesy napełniania i pakowania. Gęstość cieczy będzie ogromnym wyznacznikiem przy wyborze odpowiednich maszyn do zakupu i instalacji. Używanie sprzętu o niewłaściwym poziomie lepkości może znacznie obniżyć produktywność i zwiększyć prawdopodobieństwo wystąpienia awarii. Rozważ, czy ciecz jest rozrzedzona jak woda, gęstsza lub bardzo lepka, co można określić za pomocą lepkości chart przy wyborze maszyn.
Monitorowanie lepkości w czasie rzeczywistym ma kilka zaletoring i kontrola linii pakującej produkty płynne/płynne:
Precyzyjne i wydajne operacje linii pakującej - znaczące oszczędności w kosztach materiałów. Kontrola lepkości sprawia, że linie do pakowania płynów są bardziej „dokładne”, zapewniając spójny produkt, a tym samym umożliwia ściślejszą kontrolę odpowiedniego poziomu produktu do dozowania. Kontrola jakości lepkości na etapach produkcji i transportu, poprzedzająca operacje napełniania, może zapewnić dozowanie dokładnej ilości cieczy przy minimalnej ilości zmienności procesu, która może ewentualnie wynikać z wyposażenia linii pakującej, takiego jak dysze i zawory. Daje to firmie duże oszczędności materiałowe, biorąc pod uwagę skalę prowadzonej działalności.
Aby zachować zgodność z przepisami penalizującymi niedopełnienie, producenci często podczas produkcji przekraczają minimalną ilość w opakowaniu. Jednak takie przepełnienie bezpieczeństwa może być kosztowne. Na przykład średniej wielkości producent mleka napełnia dziennie około 100,000 XNUMX butelek mleka kokosowego. Zmniejszając przepełnienie pojedynczych butelek o kilka gramów, firma mogłaby potencjalnie zaoszczędzić kilka milionów euro rocznie. Producenci kompletnych rozlewni powinni zatem oferować systemy, które mierzą ilości napełnienia z dużą precyzją i ograniczają przepełnienie do absolutnego minimum.
Płynna zmiana produktu: zwinność w radzeniu sobie z różnymi i nowymi wariantami produktów oraz ich pochodzeniem. Inżynierowie fabryczni uzyskują dokładniejszy obraz reakcji nowych receptur lub zmian receptury oraz możliwej konieczności dostosowania bieżących systemów i parametrów kontrolnych. Monitorowanie w czasie rzeczywistymoring ułatwia przejście procesu wsadowego do pracy ciągłej, oszczędzając znaczne koszty operacyjne i kapitałowe poprzez ponowne wykorzystanie tych samych linii dla wielu produktów. Inżynierowie linii pakującej mogą szybko reagować na stale zmieniające się wymagania konsumentów, optymalizować wydajność i redukować koszty systemu.
Źródło: Pepsico Inc.
Dane dotyczące lepkości pomagają inżynierom linii pakującej dostosować parametry, aby zapewnić ścisłą kontrolę procesu dozowania, na który nie mają wpływu zmiany właściwości produktu, zwłaszcza płynność, która jest zależna od lepkości. Dodatkowo decyzje o dostosowaniu parametrów i zmiennych maszyny (dysze, pompy, sterowanie zaworami) mogą być niezawodnie napędzane i zautomatyzowane na podstawie danych o lepkości, zapewniając tym samym ograniczenie czasu przezbrojenia do minimum.
Zgodność z przepisami. Jeśli chodzi o produkty spożywcze i napoje, jakość, bezpieczeństwo i zaufanie są absolutnie krytyczne. Dokładność i powtarzalność procesu dozowania musi być ściśle kontrolowana, ponieważ normy UE, WHO i inne wytyczne GMP określają dopuszczalne poziomy tolerancji w zależności od rodzaju produktu / branży. Wyzwanie dla wszystkich tych procesów jest takie samo: opakowanie musi zawierać określoną ilość produktu. Na przykład, jeśli ilość w butelkach jest zbyt mała, jest to sprzeczne z dyrektywą UE w sprawie opakowań 76/211 / EWG i niemiecką ustawą o produktach w opakowaniach jednostkowych (§22 FPackV). Określają one procent, o jaki partia produkcyjna może być niższa od określonej minimalnej ilości napełnienia. W tym przypadku „niewłaściwe postępowanie” może prowadzić do kar, które obejmują wstrzymanie produkcji.
Oznacza to, że automatyzacja lepkości ma kluczowe znaczenie dla zapewnienia wydajności procesu napełniania i uniknięcia ryzyka związanego z odpadami, odrzutami i karami - które mogą być znacznie wysokie w fabrykach ciągłego napełniania płynami, które pakują tony materiałów na godzinę!
Inne Rozważania dotyczące wydajności ciecz linia pakująca
Łatwość czyszczenia. Kolejnym ważnym aspektem jest możliwość łatwego i bezproblemowego czyszczenia sprzętu. Im łatwiejsze jest czyszczenie maszyn, tym mniej czasu potrzeba na czyszczenie części i maszyn i tym szybciej można je ponownie uruchomić. Maszyny, które można łatwo zdemontować, pomogą utrzymać efektywny proces czyszczenia. Jednym z przykładów jest zakup przez klienta sprzętu, który oferuje ręczne lub automatyczne czyszczenie na miejscu (CIP), które jest najbardziej wydajnym sposobem czyszczenia wypełniacza. CIP przepuści roztwór czyszczący przez maszynę, aby upewnić się, że wszystkie zwilżone części są czyste.
Źródło obrazu: TetraPak
Łatwość elastyczność, zmiana i skalowalność. Łatwość zmiany i elastyczność maszyny są również integralną częścią wydajnego systemu pakowania. Oznacza to, że sprzęt powinien być w stanie pomieścić wiele typów pojemników lub płynów bez konieczności wymiany części. Niektórzy producenci mają maszyny, które są w stanie obsługiwać butelki o różnych rozmiarach przy użyciu jednego urządzenia, o ile lepkość cieczy jest stała. Maszyny powinny być również łatwe w modernizacji, co jest szczególnie ważne w miarę rozwoju firmy.
Kluczowa wartość rozwiązań automatyzacji lepkości w linii pakującej
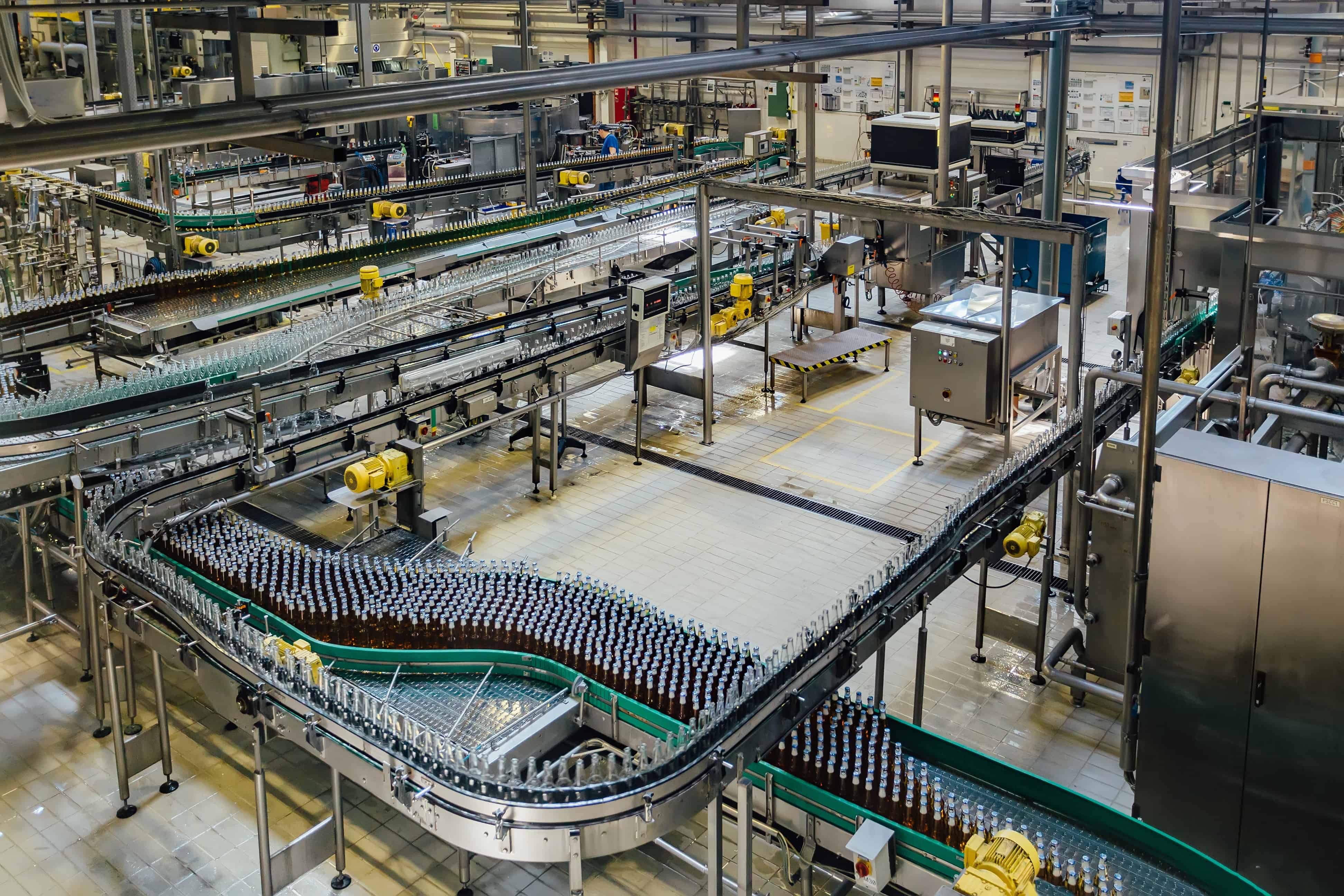
Szerokie i istotne czynniki, które sprawiają, że zarządzanie lepkością jest ważne w praktycznie każdym zastosowaniu do napełniania:
- Jakość: Monitor lepkościoring płynnego produktu na etapach przetwarzania i transportu poprzedzających operację napełniania może zapewnić, że przed napełnieniem jakość/konsystencja produktu będzie odpowiednia.
- Powtarzalność w partiach: Aby zapewnić spójność każdej partii i utrzymać stały poziom / wagę, niezbędna jest kontrola lepkości.
- Zmniejszone odpady i oszczędności kosztów: Dokładne operacje napełniania oznaczają, że dokładna ilość produktu jest dostarczana podczas pakowania, co pozwala zaoszczędzić tony dodatkowych materiałów, które w przeciwnym razie mogłyby zostać dodatkowo wykorzystane. Oznacza to również zmniejszenie ilości odpadów i odrzutów, nawet w najsurowszych przepisach, minimalizując w ten sposób koszty.
- Wydajność: Bezproblemowy monitoring w czasie rzeczywistymoring lepkości może zaoszczędzić wiele czasu i wysiłku związanego z analizą próbki offline i podejmowaniem decyzji procesowych na podstawie tej analizy.
- Środowisko: Automatyzacja lepkości może zoptymalizować procesy CIP / SIP. Zmniejszenie ilości płynów / materiałów czyszczących jest dobre dla środowiska.
- Inteligentna fabryka - korzyści z digitalizacji i automatyzacji: Dane procesowe zebrane przez czujniki mogą być wykorzystywane na wiele innych sposobów - planowanie konserwacji maszyn, diagnostyka kontroli jakości, analiza przyczyn źródłowych, wymiana informacji między obiektami w celu decentralizacji decyzji i wiele innych. Możliwość ładowania różnych zadań / modeli dla różnych płynów za pomocą informacji o lepkości przekształca się w korzyści o pierwszorzędnym znaczeniu, umożliwiając firmom czerpanie korzyści z Przemysłu 4.0 i technologii automatyzacji. Stają się bardziej przystosowalne do ciągle zmieniających się potrzeb konsumentów. Dowiedz się więcej, korzystając z poniższego łącza.
Cyfrowe przetwarzanie żywności - siła napędowa dla producentów na rzecz Przemysłu 4.0
Wahania temperatury, stan sprzętu do mieszania, rodzaj i warunki podłoży, receptury rzadkiego ciasta, interakcje między etapami procesu i parametry czasu mieszania mogą wpłynąć na jakość produktu i jego wydajność w różnych partiach podczas mieszania i powlekania ciasta. W sektorach o niewielkich marżach, takich jak pieczywo, żywność w panierce i wyroby cukiernicze,…
Pomiar lepkości i wyzwania procesowe
Inżynierowie i operatorzy instalacji na liniach pakujących zdają sobie sprawę z potrzeby dokonywania pomiarów lepkości i interwencji poprzez odpowiednie działania korygujące w celu uzyskania wysokiej jakości i stałej, przewidywalnej sypkości produktu płynnego / półpłynnego. Jednak dokonywanie tych pomiarów przez lata stanowiło dla nich wyzwanie.
Pobrane próbki offline są po prostu zawodne i nie nadają się do operacji pakowania płynów
Monitoring lepkość płynu w procesie często oznacza pobranie próbki płynu ze zbiornika lub rurociągu i dostarczenie próbki do laboratorium, gdzie jej właściwości płynięcia i reologiczne są mierzone za pomocą wiskozymetru laboratoryjnego lub reometru. Na podstawie wyników należy poinformować operatora procesu, czy płyn ma pożądaną lepkość, lub jeśli wymagane są dalsze działania, po interwencji należy wykonać nowe pomiary. System ten nazywany jest sterowaniem off-line lub ręcznym i ma kilka oczywistych wad – jest czasochłonny i często niedokładny nawet w przypadku doświadczonych operatorów. Najczęściej wyniki są zbyt późne, aby zapisać partię.
Alternatywą jest użycie wbudowanego wiskozymetru, który będzie stale monitorował lepkość płynu procesowego w trakcie całego procesu. Ten instrument daje sygnał wyjściowy, który, jeśli jest wyświetlany, dostarcza operatorowi informacji niezbędnych do sterowania procesem. Alternatywnie, wyjścia lepkościomierza są podłączone do PLC (sterownik programowalny) / DCS (cyfrowy system sterowania) w celu automatycznego sterowania procesem.
Problemy z konwencjonalnymi lepkościomierzami do instalacji liniowej
Tradycyjne wiskozymetry procesowe napotykają problemy związane z przepływem płynu w rurociągach i instalacjach mieszania zbiorników. Ogólnie rzecz biorąc, te wiskozymetry starszej generacji nie działają prawidłowo w przepływie turbulentnym. Instrumenty obrotowe działają tylko do pewnego maksymalnego natężenia przepływu. Przepływ musi być kontrolowany dla lepkościomierzy spadku ciśnienia. W przypadku tych typów problemów związanych z przepływem można uniknąć, instalując lepkościomierz na linii obejściowej i dostosowując przepływ próbki do urządzenia. Czas reakcji przyrządu jest wtedy powiązany z warunkami przepływu, ponieważ do skutecznej kontroli wymagana jest odpowiednia szybkość wymiany próbki. Ponadto instrumenty używane w środowisku procesowym muszą być solidne i odporne na wszelkie korozyjne materiały, z którymi mogą się zetknąć, zwłaszcza podczas czyszczenia.
RheonicsRozwiązania poprawiające wydajność i elastyczność linii pakującej
Zautomatyzowany pomiar i kontrola lepkości na linii ma kluczowe znaczenie dla monitorowania/kontroli lepkości podczas operacji napełniania i zapewnienia dostosowania parametrów maszyny linii pakującej w zależności od lepkości produktu. Rheonics oferuje następujące rozwiązania w zakresie kontroli procesu i optymalizacji wydajności linii pakującej.
Mierniki lepkości i gęstości
- In-line Lepkość pomiary: Rheonics" SRV to szerokozakresowe urządzenie do pomiaru lepkości w linii, umożliwiające pomiary lepkości (wraz z pomiarami temperatury) i wykrywanie zmian lepkości w dowolnym strumieniu procesowym w czasie rzeczywistym.
- In-line Lepkość i gęstość pomiary: Rheonics" SRD jest przyrządem do jednoczesnego pomiaru gęstości i lepkości w linii (wraz z pomiarem temperatury). Jeśli pomiar gęstości jest ważny dla twoich operacji, SRD może zaspokoić twoje potrzeby, oferując możliwości operacyjne podobne do SRV, a także dokładne pomiary gęstości.
Instrument ten daje sygnał wyjściowy i odczytuje na panelu oprogramowania, który, jeśli jest wyświetlany, dostarcza operatorowi informacji niezbędnych do sterowania procesem. Alternatywnie może być możliwe wysłanie wyjścia do automatycznego sterownika procesu. Zintegrowane systemy sterowania umożliwiają efektywne wykorzystanie informacji o lepkości / gęstości w linii technologicznej.
Zintegrowane, gotowe pod klucz jakość i konserwacjami do obsługi linii rozlewniczych
Rheonics oferuje zintegrowane rozwiązanie „pod klucz” do zarządzania jakością, składające się z:
- In-line Lepkość pomiary: Rheonics'SRV - szerokozakresowy, wbudowany miernik lepkości z wbudowanym pomiarem temperatury płynu
- Rheonics Monitor procesu: zaawansowany predykcyjny kontroler śledzenia do monitorowania i kontrolowania zmian warunków procesu w czasie rzeczywistym
- Rheonics RheoPulse , , , , , , , , , , , , ,, ,, ,, ,, ,, ,, ,, ,, ,, ,, ,, ,, ,, ,, ,, ,, ,, ,, ,, ,, ,, ,, ,, ,, ,, ,, ,, ,, ,, ,, ,, ,, , w automatyczny dOsing: Autonomiczny system poziomu 4, który zapewnia brak kompromisów przy ustalonych granicach lepkości i automatycznie aktywuje zawory obejściowe lub pompy w celu adaptacyjnego dozowania składników mieszanki na etapach przetwarzania poprzedzających operacje napełniania.
Rheonics Monitor procesu
Czujnik SRV jest umieszczony w linii, więc w sposób ciągły mierzy lepkość (i gęstość w przypadku SRD). Alerty można skonfigurować tak, aby powiadamiały operatora o niezbędnych działaniach lub cały proces zarządzania można w pełni zautomatyzować za pomocą RPTC (Rheonics Predykcyjny kontroler śledzenia). Zastosowanie SRV na linii rozlewniczej skutkuje poprawą produktywności, marży zysku i zapewnia zgodność z przepisami. Rheonics Czujniki mają kompaktową obudowę, co ułatwia instalację OEM, modernizację i łatwe skalowanie na wszystkich liniach w fabryce. Nie wymagają konserwacji ani ponownej konfiguracji. Czujniki zapewniają dokładne, powtarzalne wyniki niezależnie od sposobu i miejsca montażu, bez konieczności stosowania specjalnych komór, uszczelek gumowych lub zabezpieczeń mechanicznych. Nie wykorzystujące materiałów eksploatacyjnych i nie wymagające ponownej kalibracji, SRV i SRD są niezwykle łatwe w obsłudze, co skutkuje wyjątkowo niskimi kosztami eksploatacji w całym okresie użytkowania. Jako konstruktor maszyn lub integrator systemów automatyki możesz dowiedzieć się więcej o łatwości integracji rheonics czujnika w Twojej linii na naszej dedykowanej stronie dla integratorów systemów.
Po ustaleniu środowiska procesowego zwykle nie potrzeba wiele wysiłku, aby utrzymać spójność integralności systemów – operatorzy mogą polegać na ścisłej kontroli dzięki Rheonics rozwiązanie do zarządzania linią pakowania płynów.
Gęstościomierze typu inline mają przewagę w automatycznym napełnianiu na podstawie wagi
W przypadku precyzyjnego automatycznego napełniania (na przykład - metoda wolumetryczna) szczególnie ważne może być monitorowanie i kontrolowanie gęstości. Gęstość może się zmieniać z powodu pęcherzyków powietrza w cieczy i zmian temperatury lub receptury.
Przepływomierze Coriolisa wykonują pomiary przepływu masowego, ale mają pewne wady, takie jak:
- Czasochłonne procedury kalibracji i trudna instalacja
- Trudności w czyszczeniu: przepływomierze Coriolisa są trudne do czyszczenia, zwłaszcza gdy płyn zawiera znaczną zawartość części stałych. To sprawia, że nie spełniają norm higienicznych wewnątrz fabryk.
- Dłuższe czasy napełniania: w przypadku technologii ważenia lub pomiaru przepływu masowego napełnienie butelki zajmuje około pięciu sekund. Pomiar natężenia przepływu podlega największej fluktuacji prędkości napełniania, przy czym czas waha się od dwóch do pięciu sekund.
Z drugiej strony, Rheonics SRD zostały zaprojektowane i zbudowane z myślą o najłatwiejszej integracji w ciągłym środowisku produkcyjnym. Nie mają specjalnych komór i można je łatwo wyjąć w celu czyszczenia lub kontroli. Sondy SRD są hermetycznie uszczelnione w celu czyszczenia na miejscu (CIP) i obsługują mycie pod wysokim ciśnieniem za pomocą złączy IP69K M12. SRD to unikalny produkt, który zastępuje trzy różne przyrządy do pomiaru lepkości, gęstości i temperatury.
Linie pakujące może najlepiej wykorzystać postęp w technologii automatyzacji poprzez Rheonics
Rheonics systemy automatyzacji obejmują funkcje wykraczające poza dotychczasowe systemy, takie jak wbudowane zaawansowane algorytmy sterowania procesami, monitorowanie statystyczneoring, monitorowanie urządzenia inteligentnegooring i monitor kondycji aktywóworing. Dostarczają dane o procesach i stanie aktywów zarówno do operacji, jak i konserwacji, umożliwiając nowe i wydajne sposoby integracji procesów pracy oraz poprawiając terminowość i dokładność decyzji, co ma kluczowe znaczenie, biorąc pod uwagę szybkość i skalę operacji na linii pakowania produktów płynnych.
Zwiększanie inteligencji systemów CIP
Rheonics SRV (i SRD) są nie tylko zgodne z CIP/SIP, ale także monitorują czyszczenie przewodów cieczy za pomocą monitoring lepkość (i gęstość) środka czyszczącego/rozpuszczalnika podczas fazy czyszczenia. Czujnik wykrywa wszelkie drobne pozostałości, umożliwiając operatorowi podjęcie decyzji, czy linia jest czysta/odpowiednia. Alternatywnie SRV (i SRD) dostarcza informacje do zautomatyzowanego systemu czyszczenia, aby zapewnić pełne i powtarzalne czyszczenie pomiędzy seriami, zapewniając w ten sposób pełną zgodność z normami sanitarnymi zakładów produkujących żywność/farmaceutyki. Dowiedz się więcej o tym, jak to zrobić rheonics systemy lepkości optymalizują systemy CIP, aby skrócić czas czyszczenia/przestoje. Oznacza to również znaczne oszczędności w zakresie płynów/materiałów czyszczących. Więcej szczegółów w jaki sposób SRV jest kompatybilny z CIP, a jednocześnie lepiej pomaga zoptymalizować proces CIP.
Rheonics' Korzyść
Kompaktowy kształt, brak ruchomych części i nie wymaga konserwacji
Rheonics' SRV i SRD mają bardzo małe wymiary, co ułatwia instalację OEM i modernizację. Umożliwiają łatwą integrację z dowolnym strumieniem procesu. Są łatwe w czyszczeniu i nie wymagają konserwacji ani ponownej konfiguracji. Mają niewielką powierzchnię, co pozwala na instalację Inline w dowolnej linii technologicznej, bez konieczności stosowania dodatkowej przestrzeni lub adaptera.
Higieniczny, sanitarny projekt
Rheonics SRV i SRD są dostępne w tri-clamp i DIN 11851 oprócz niestandardowych przyłączy procesowych.
Zarówno SRV, jak i SRD są zgodne z wymogami dotyczącymi kontaktu z żywnością zgodnie z przepisami amerykańskiej FDA i UE.
Wysoka stabilność i niewrażliwość na warunki montażu: Możliwa dowolna konfiguracja
Rheonics SRV i SRD wykorzystują unikalny, opatentowany rezonator współosiowy, w którym dwa końce czujników skręcają się w przeciwnych kierunkach, eliminując momenty reakcji podczas ich montażu, a tym samym czyniąc je całkowicie niewrażliwymi na warunki montażu i natężenia przepływu. Element czujnika znajduje się bezpośrednio w płynie, bez konieczności stosowania specjalnej obudowy lub klatki ochronnej.
Natychmiastowe dokładne odczyty „płynności” - Pełny przegląd systemu i sterowanie predykcyjne
Rheonics" RheoPulse , , , , , , , , , , , , ,, ,, ,, ,, ,, ,, ,, ,, ,, ,, ,, ,, ,, ,, ,, ,, ,, ,, ,, ,, ,, ,, ,, ,, ,, ,, ,, ,, ,, ,, ,, ,, , oprogramowanie jest wydajne, intuicyjne i wygodne w użyciu. Płyn procesowy w czasie rzeczywistym może być monitorowany na zintegrowanym IPC lub komputerze zewnętrznym. Wiele czujników rozmieszczonych w całym zakładzie jest zarządzanych z jednej tablicy rozdzielczej. Brak wpływu pulsacji ciśnienia pompowania na działanie czujnika lub dokładność pomiaru. Brak efektu wibracji.
Pomiary w linii, nie jest wymagana linia obejściowa
Zainstaluj czujnik bezpośrednio w strumieniu procesowym, aby wykonywać pomiary lepkości (i gęstości) w czasie rzeczywistym. Nie jest wymagana linia obejściowa: czujnik można zanurzyć w linii; natężenie przepływu i wibracje nie wpływają na stabilność i dokładność pomiaru.
Łatwa instalacja i brak konieczności ponownej konfiguracji / ponownej kalibracji - zero konserwacji / przestojów
W mało prawdopodobnym przypadku uszkodzenia czujnika należy wymienić czujniki bez wymiany lub ponownego programowania elektroniki. Doraźne zamienniki zarówno czujnika, jak i elektroniki, bez aktualizacji oprogramowania sprzętowego i zmian kalibracji. Łatwy montaż. Dostępne ze standardowymi i niestandardowymi przyłączami procesowymi, takimi jak NPT, Tri-Clamp, DIN 11851, kołnierzowe, Varinline i inne przyłącza sanitarne i higieniczne. Żadnych specjalnych komór. Łatwe do usunięcia w celu czyszczenia lub kontroli. SRV jest również dostępny w wersji DIN11851 i tri-clamp złącze ułatwiające montaż i demontaż. Sondy SRV są hermetycznie uszczelnione w celu czyszczenia na miejscu (CIP) i obsługują mycie pod wysokim ciśnieniem za pomocą złączy IP69K M12.
Rheonics przyrządy posiadają sondy ze stali nierdzewnej i opcjonalnie posiadają powłoki ochronne w sytuacjach specjalnych.
Niskie zużycie energii
Zasilacz 24 V DC o poborze prądu mniejszym niż 0.1 A podczas normalnej pracy.
Krótki czas reakcji i lepkość kompensowana temperaturą
Ultraszybka i solidna elektronika w połączeniu z kompleksowymi modelami obliczeniowymi sprawia, że Rheonics urządzenia jedne z najszybszych, wszechstronnych i najdokładniejszych w branży. SRV i SRD umożliwiają dokładne pomiary lepkości (i gęstości w przypadku SRD) w czasie rzeczywistym co sekundę i nie mają na nie wpływu zmiany natężenia przepływu!
Szerokie możliwości operacyjne
RheonicsPrzyrządy są zbudowane tak, aby wykonywać pomiary w najtrudniejszych warunkach.
SRV jest dostępny z najszerszy na rynku zakres działania wiskozymetru procesowego w linii:
- Zakres ciśnienia do 5000 psi
- Zakres temperatur od -40 do 200 ° C
- Zakres lepkości: od 0.5 cP do 50,000 cP (i więcej)
SRD: Pojedynczy instrument, potrójna funkcja - Lepkość, temperatura i gęstość
Rheonics' SRD to unikalny produkt, który zastępuje trzy różne przyrządy do pomiarów lepkości, gęstości i temperatury. Eliminuje trudności związane ze zlokalizowaniem trzech różnych instrumentów i zapewnia niezwykle dokładne i powtarzalne pomiary w najtrudniejszych warunkach.
zarządzanie dozowanie / napełnianie wydajniej, obniżyć koszty i zwiększyć produktywność
Zintegruj SRV z linią procesową i zapewnij spójność przez lata. SRV stale monitoruje i kontroluje lepkość (i gęstość w przypadku SRD) oraz aktywuje zawory adaptacyjnie do dozowania składników mieszanki. Zoptymalizuj proces za pomocą SRV i doświadcz mniej przestojów, mniejszego zużycia energii, mniej niezgodności i oszczędności kosztów materiałów. A na koniec przyczynia się do lepszych wyników finansowych i lepszego środowiska!
Czyszczenie na miejscu (CIP) i sterylizacja na miejscu (SIP)
SRV (i SRD) monitoruje czyszczenie przewodów cieczy za pomocą monitoring lepkość (i gęstość) środka czyszczącego/rozpuszczalnika podczas fazy czyszczenia. Czujnik wykrywa wszelkie drobne pozostałości, umożliwiając operatorowi podjęcie decyzji, czy linia jest czysta/odpowiednia. Alternatywnie SRV (i SRD) dostarcza informacje do zautomatyzowanego systemu czyszczenia, aby zapewnić pełne i powtarzalne czyszczenie pomiędzy seriami, zapewniając w ten sposób pełną zgodność z normami sanitarnymi obowiązującymi w zakładach produkujących żywność.
Co to jest CIP? Optymalizacja systemów CIP (Clean In Place) z wbudowanymi pomiarami lepkości i gęstości
Co to jest CIP? W systemach CIP czyszczenie odbywa się bez demontażu systemu. CIP odnosi się do wszystkich tych systemów mechanicznych i chemicznych, które są niezbędne do przygotowania sprzętu do przetwarzania żywności, albo po przebiegu przetwarzania, który przyniósł normalne…
Doskonała konstrukcja i technologia czujnika
Mózgiem tych czujników jest wyrafinowana, opatentowana elektronika. SRV i SRD są dostępne ze standardowymi przyłączami procesowymi, takimi jak ¾” NPT, DIN 11851, kołnierzowe i Tri-clamp umożliwiając operatorom wymianę istniejącego czujnika temperatury w linii technologicznej na SRV/SRD, dostarczając bardzo cennych i przydatnych informacji o płynie procesowym, takich jak lepkość, oprócz dokładnego pomiaru temperatury za pomocą wbudowanego czujnika Pt1000 (dostępna klasa AA, A, B DIN EN 60751) .
Elektronika zbudowana tak, aby pasowała do Twoich potrzeb
Dostępna zarówno w obudowie przetwornika, jak i małej obudowie do montażu na szynie DIN, elektronika czujnika umożliwia łatwą integrację z liniami procesowymi i wewnątrz szaf maszynowych.
Łatwa integracja
Wiele analogowych i cyfrowych metod komunikacji zaimplementowanych w elektronice czujnika sprawia, że podłączenie do przemysłowych sterowników PLC i systemów sterowania jest proste i proste.
Opcje komunikacji analogowej i cyfrowej
Opcjonalne opcje komunikacji cyfrowej
Zgodność z ATEX i IECEx
Rheonics oferuje czujniki iskrobezpieczne z certyfikatami ATEX i IECEx do stosowania w środowiskach niebezpiecznych. Czujniki te spełniają zasadnicze wymagania bezpieczeństwa i higieny pracy związane z projektowaniem i konstrukcją urządzeń i systemów ochronnych przeznaczonych do stosowania w przestrzeniach zagrożonych wybuchem.
Posiadane przez firmę certyfikaty iskrobezpieczności i przeciwwybuchowości Rheonics pozwala także na dostosowanie istniejącego czujnika, pozwalając naszym klientom uniknąć czasu i kosztów związanych z identyfikacją i testowaniem alternatywy. Można dostarczyć czujniki niestandardowe do zastosowań wymagających od jednej jednostki do tysięcy jednostek; z czasem realizacji wynoszącym tygodnie zamiast miesięcy.
Rheonics SRV & SRD posiadają zarówno certyfikat ATEX, jak i IECEx.
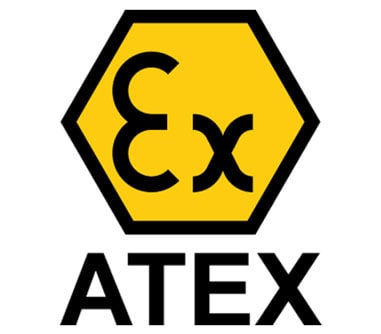
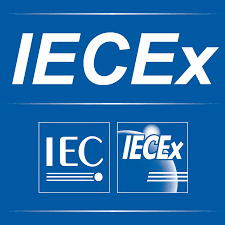
Realizacja
Zainstaluj czujnik bezpośrednio w strumieniu procesowym, aby wykonywać pomiary lepkości i gęstości w czasie rzeczywistym. Nie jest wymagana linia obejściowa: czujnik można zanurzyć w linii; natężenie przepływu i wibracje nie wpływają na stabilność i dokładność pomiaru. Zoptymalizuj wydajność mieszania, zapewniając powtarzalne, kolejne i spójne testy płynu.
Lokalizacje kontroli jakości w linii
- W czołgach
- W rurach łączących między różnymi pojemnikami procesowymi
Instrumenty / czujniki
SRV Wiskozymetr LUB an SRD dla dodatkowej gęstości
Rheonics Wybór instrumentu
Rheonics projektuje, produkuje i sprzedaje innowacyjne czujniki i monitory płynóworing systemy. Precyzja zbudowana w Szwajcarii, RheonicsWiskozymetry i gęstościomierze in-line charakteryzują się czułością wymaganą w danym zastosowaniu i niezawodnością niezbędną do przetrwania w trudnych warunkach operacyjnych. Stabilne wyniki – nawet w niekorzystnych warunkach przepływu. Brak wpływu spadku ciśnienia lub natężenia przepływu. Równie dobrze nadaje się do pomiarów kontroli jakości w laboratorium. Nie ma potrzeby zmiany żadnego komponentu ani parametru, aby mierzyć w pełnym zakresie.
Sugerowane produkty do zastosowania
- Szeroki zakres lepkości - monitoruj cały proces
- Powtarzalne pomiary zarówno płynów newtonowskich, jak i nienewtonowskich, płynów jednofazowych i wielofazowych
- Hermetycznie zamknięte, wszystkie części ze stali nierdzewnej 316L zwilżane
- Wbudowany pomiar temperatury płynu
- Kompaktowy kształt ułatwiający instalację w istniejących liniach technologicznych
- Łatwy w czyszczeniu, nie wymaga konserwacji ani ponownej konfiguracji
- Pojedynczy przyrząd do pomiaru gęstości procesowej, lepkości i temperatury
- Powtarzalne pomiary zarówno płynów newtonowskich, jak i nienewtonowskich, płynów jednofazowych i wielofazowych
- Konstrukcja wykonana w całości z metalu (stal nierdzewna 316L)
- Wbudowany pomiar temperatury płynu
- Kompaktowy kształt ułatwiający montaż w istniejących rurach
- Łatwy w czyszczeniu, nie wymaga konserwacji ani ponownej konfiguracji