Monitoring oraz kontrolowanie lepkości w formułowaniu, testowaniu i stosowaniu klejów i uszczelniaczy
Wprowadzenie
Kleje i szczeliwa są szeroko stosowane do łączenia, ochrony i uszczelniania systemów w budownictwie, produkcji i konserwacji.
Branża ta stoi przed wyzwaniami związanymi z ograniczonymi surowcami (rezerwami ropy) oraz negatywnym wpływem związków syntetycznych na zdrowie ludzi i środowisko. Kluczowe surowce używane do produkcji klejów pochodzą z ropy naftowej i produktów petrochemicznych. Wahania cen tych produktów wpływały w ostatnich latach na rentowność uczestników. Liderzy branży zmierzają w kierunku przyjęcia bardziej zaawansowanych technologii, takich jak automatyzacja, przemysłowy internet rzeczy (IIoT) i techniki symulacji, i podejmują różne strategiczne inicjatywy, takie jak szeroko zakrojone działania badawczo-rozwojowe na rzecz zrównoważonej produkcji i opłacalnych operacji.
Zastosowania przemysłowe i informacje o rynku klejów i uszczelniaczy
Różne sektory i branże wykorzystują kleje w ramach swoich procesów.
- kleje jako system zamykania w branży opakowań,
- kleje jako system do budowy skomplikowanych konstrukcji, takich jak drapacze chmur, samoloty, pociągi lub autobusy.
- Montaż samochodowy (przyklejanie dywanów, deski rozdzielczej, siedzeń itp.),
- ogólne wytwarzanie, takie jak klejenie ekranów iPhone'ów,
- produkcja elektroniki, produkcja ogniw słonecznych,
- produkcja okien i drzwi.
Wielkość rynku klejów i uszczelniaczy szacuje się na 58.9 mld USD w 2019 r. I przewiduje się, że osiągnie 73.8 mld USD do 2024 r., Przy CAGR wynoszącym 4.6%, od 2019 do 2024 r. Rynki i rynki). Rosnące wykorzystanie klejów i uszczelniaczy w różnych zastosowaniach, takich jak papier i opakowania, budownictwo i budownictwo, obróbka drewna, konsument / majsterkowanie, motoryzacja i transport, skóra i obuwie, montaż i inne napędzają wzrost rynku klejów i uszczelniaczy.
Oczekuje się, że segment motoryzacyjno-transportowy będzie rósł w najwyższym CAGR pod względem wartości w latach 2019-24 dzięki wzrostowi popytu na samochody lekkie, wydajne i ekologiczne. Rosnące zapotrzebowanie na kleje i uszczelniacze w szybko rozwijających się Indiach, Chinach, Korei Południowej, Malezji, Wietnamie, Tajwanie, Indonezji, między innymi w regionie, przyspiesza rozwój rynku klejów i uszczelniaczy na całym świecie.
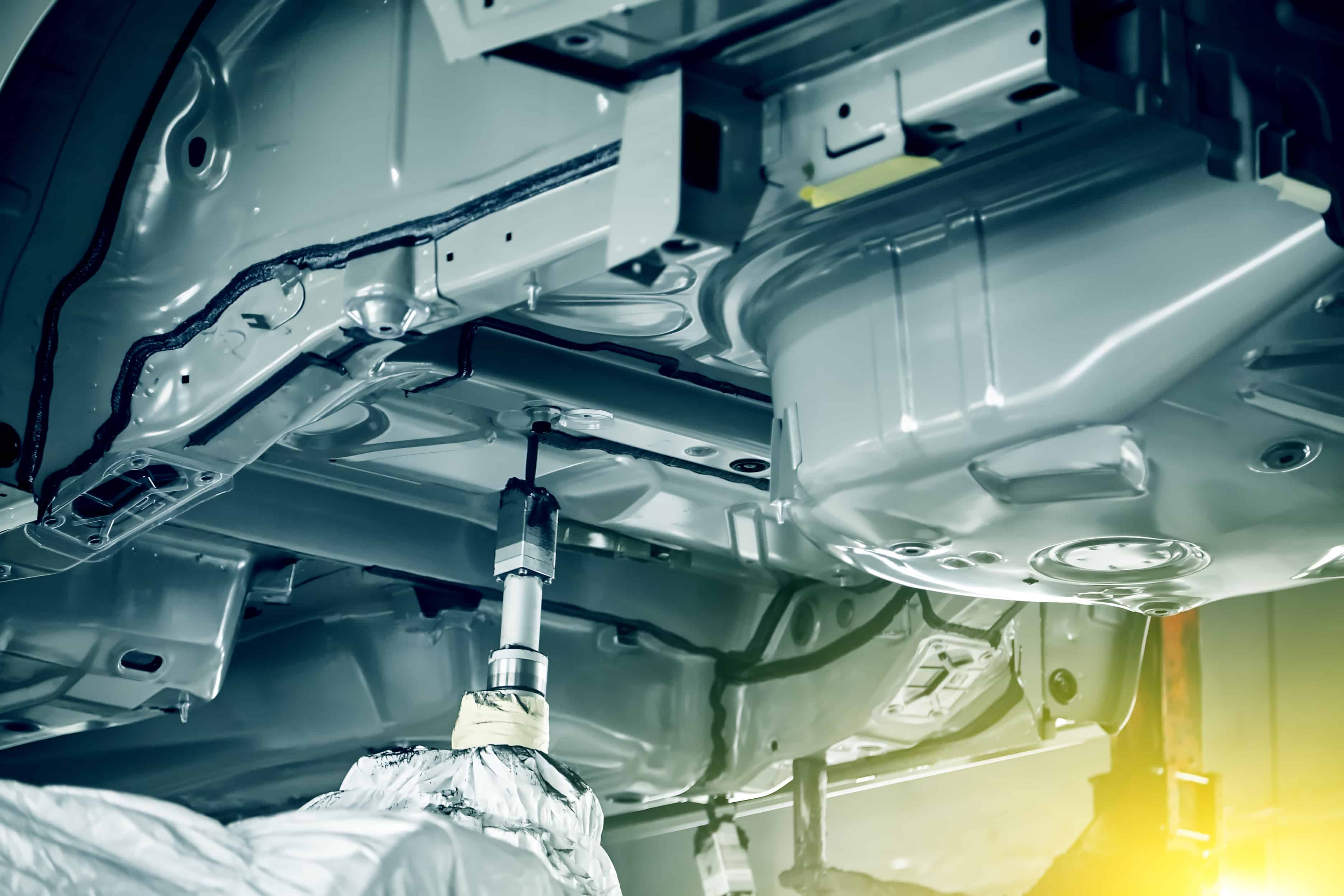
Zastosowanie
Nowa gama klejów przemysłowych o wysokiej wytrzymałości jest obecnie stosowana w przemyśle motoryzacyjnym oraz w innych operacjach produkcyjnych jako zamiennik do zgrzewania punktowego, mechanicznych elementów złącznych i innych tradycyjnych metod łączenia. Kleje oferują kilka głównych zalet w porównaniu z konwencjonalnymi technikami mocowania, w tym bardziej jednolitą siłę wiązania na większej powierzchni, w porównaniu do miejscowych punktów wytrzymałości zwykle uzyskiwanych przy mocowaniu mechanicznym. Kleje są używane do łączenia powierzchni, zazwyczaj poprzez zmianę ich fazy z ciekłej na stałą. Czasami jest to wywoływane zmianą temperatury (kleje topliwe), w innych przypadkach klej twardnieje w warunkach otoczenia (kleje kontaktowe) np. Z powodu odparowania rozpuszczalnika lub wilgoci otaczającego powietrza.
Kompozycja
Kleje i szczeliwa są złożonymi formułami stosowanymi do wiązania podłoży lub uszczelniania połączeń lub szczelin. Występują w różnych postaciach, ale są zwykle dyspersjami zawierającymi materiały polimerowe lub środki utwardzające, środki powierzchniowo czynne i rozpuszczalniki. Kleje mogą być reaktywne lub niereaktywne. W przypadku klejów reaktywnych przyczepność może być indukowana przez zmieszanie dwóch lub więcej składników reaktywnych, takich jak żywica epoksydowa i utwardzacz, lub może być indukowana przez bodźce zewnętrzne, takie jak promieniowanie UV, ciepło lub wilgoć. W przypadku niereaktywnych klejów przyczepność jest indukowana przez bodźce fizyczne, takie jak na przykład ciśnienie lub odparowanie rozpuszczalnika. W przypadku szczeliwa podstawową funkcją jest uszczelnianie połączeń lub szczelin i zapobieganie przedostawaniu się wilgoci, rozpuszczalników lub gazów do układu lub komponentu lub ucieczce z niego, chociaż wiele uszczelniaczy może pełnić wiele funkcji.
Większość klejów i uszczelniaczy składa się z materiałów polimerowych lub zawiera monomery lub oligomery, które po reakcji tworzą usieciowaną sieć polimerową. W konsekwencji masa cząsteczkowa i struktura cząsteczkowa tych składników są krytyczne dla właściwości materiału zarówno przed, jak i po adhezji. Wiele preparatów klejących i uszczelniających to układy dwufazowe, które obejmują emulsje zawierające zdyspergowany polimer lub zdyspergowane ciała stałe w przypadku uszczelnienia. W obu przypadkach wielkość cząstek i wielkość kropelek mogą mieć kluczowe znaczenie dla działania produktu.
Każdy, kto zamierza stosować kleje i szczeliwa, musi zmierzyć się z ogromnym wyzwaniem, jakim jest właściwy wybór materiału, a także określenie właściwych procesów. Klej lub szczeliwo musi spłynąć na powierzchnię podłoża, a następnie zmienić płynną ciecz w strukturalne ciało stałe, nie powodując szkodliwych naprężeń wewnętrznych w złączu. Wiele ewoluujących problemów z klejem lub uszczelniaczem nie wynika z niewłaściwego wyboru materiału lub konstrukcji złącza, ale są bezpośrednio związane z wadliwymi technikami produkcji, w większości pozbawionymi odpowiedniej kontroli procesu.
Dlaczego pomiar lepkości jest ważny przy przygotowywaniu preparatów?
Istnieje wiele rodzajów klejów i uszczelniaczy, które należy wziąć pod uwagę przy konfigurowaniu procesu produkcyjnego. Staranne rozważenie lepkości pomaga wybrać odpowiedni materiał zarówno do projektu produktu, jak i procesu produkcyjnego wymaganego do jego zbudowania.
Nowoczesne kleje są często złożoną formułą składników spełniających specjalne funkcje. Formułowanie surowców w użyteczne systemy klejenia i uszczelniania samo w sobie jest szeroką dziedziną technologii. Kleje i szczeliwa mogą być wytwarzane w różnych postaciach: jedno- i dwuczęściowych płynów, roztworów na bazie rozpuszczalników, emulsji na bazie wody, folii na podłożu lub bez podparcia, wstępnie uformowanych granulek lub kształtek i wielu innych postaciach. Ta różnorodność możliwości formułowania i form końcowego zastosowania wskazuje na zaawansowany stan rozwoju klejów i uszczelniaczy.
Lepkość (i reologia) jest jednym z najważniejszych parametrów w produkcji i przetwarzaniu klejów. Kolejny przychodzący materiał musi zostać przetestowany pod kątem lepkości przed użyciem (np. W systemie dozowania). Różne rozpuszczalniki, środki rozpuszczalne, proszki żywiczne lub obojętne wypełniacze mogą być stosowane do kontrolowania lepkości kleju. Lepkość systemów klejących może wymagać zwiększenia lub zmniejszenia w zależności od zastosowania i środowiska operacyjnego.
- Kontrola lepkości jest jedną z metod powszechnie stosowanych do utrzymania jednolitej grubości produktu i linii wiązania. Zagęszczacze i środki tiksotropowe są stosowane do utrzymania rozsądnej grubości linii kleju poprzez regulację lepkości.
- Charakterystykę przepływu można regulować przez włączenie wypełniacze, przez zastosowanie listew lub taśm tkanych jako „podkładek wewnętrznych” w samym kleju lub przez staranną regulację cyklu utwardzania. Wypełniacze są wprowadzane w celu kontrolowania lepkości klejów, a także innych właściwości.
- Uwięzienie powietrza może być przyczyną awarii, szczególnie w małych aplikacjach. Usunięcie powietrza z układu przed zastosowaniem może być niezbędnym etapem przetwarzania. Szczeliny powietrzne mogą uniemożliwić pełne połączenie kleju z powierzchnią podłoża, co może skutkować zmniejszoną wytrzymałością. Rozcieńczalniki zmniejszyć lepkość i skrócić czas potrzebny klejom do skutecznego zwilżenia podłoża. Zmniejszona lepkość pomaga również w usuwaniu uwięzionego powietrza i wspomaga kapilarne działanie kleju w wypełniających się porach i wnękach, które mogą znajdować się na powierzchni podłoża. Jednak dodanie rozcieńczalników, zwłaszcza nieprzereagowanych ciekłych żywic, zwykle powoduje obniżenie gęstości usieciowania, co z kolei może skutkować zmniejszoną wytrzymałością na wysoką temperaturę i niższą odpornością na środowisko.
- Proporcje mieszania dla wielu dwuczęściowych materiałów może być poważnym problemem. Niektóre systemy są bardzo wrażliwe na niewielkie zmiany proporcji mieszania. Wiele materiałów jest zrównoważonych stechiometrycznie, a mieszanka o niewłaściwym stosunku może powodować nierównomierne utwardzenie materiału i / lub pogorszenie jego optymalnej zdolności. Niektóre materiały, które nie są tak wrażliwe na proporcje mieszania, mogą wykazywać nieco inne właściwości, gdy proporcja jest zmienna. Materiały, które utwardzają się przy użyciu mieszanki nieproporcjonalnej, mogą mieć nieco inną twardość końcową i wytrzymałość na rozciąganie, co wpływa na końcową wydajność. Alternatywnym rozwiązaniem w celu spełnienia rygorystycznych wymagań dotyczących stosunku mieszania może być ciągłe monitorowanie lepkości podczas całego procesu mieszania i regulacja ilości różnych składników / materiałów w zależności od pożądanych właściwości przepływu.
- Mieszanie dwuskładnikowych klejów jest podstawową funkcją procesu, ale jest niezbędne dla prawidłowego działania tych klejów. Niewystarczająca mieszanka może spowodować częściową reakcję chemiczną, która prowadzi do częściowego utwardzenia. Niewystarczająco utwardzony materiał najprawdopodobniej spowoduje słabą siłę wiązania i niższe właściwości fizyczne. Również mieszanie oryginalnego pojemnika może być bardzo ważne. Wypełniacze lub inne składniki mogą się osadzać. Zapewnienie jednorodna mieszanka każdego składnika przed zmieszaniem (dla dwóch części) jest niezbędny do osiągnięcia maksymalnych właściwości. Pomiary lepkości w wielu punktach mieszanki mogą pomóc monitorować i regulować jednorodność do pożądanego poziomu dla aplikacji.
Powolne i krytyczne wymagania przetwarzania niektórych klejów mogą być poważną wadą, szczególnie w operacjach produkcyjnych na dużą skalę. Jeśli klej ma wiele składników, części należy dokładnie zważyć i wymieszać. Proces ustawiania często wymaga ciepła i ciśnienia. Długi czas wiązania sprawia, że przyrządy i uchwyty są niezbędne do montażu. Konieczne są również sztywne kontrole procesu, ponieważ właściwości kleju zależą od parametrów utwardzania i przygotowania powierzchni. Kontrola gotowych połączeń w celu kontroli jakości jest bardzo trudna. Wymaga to również ścisłej kontroli nad całym procesem łączenia, aby zapewnić jednolitą jakość. Nieniszczące techniki testowe nie mogą ilościowo przewidzieć wytrzymałości stawu.
Pomiary lepkości w testach
Testowanie jest niezwykle istotną funkcją w przemyśle klejów i uszczelniaczy z kilku powodów. Nie można w wiarygodny sposób przewidzieć właściwości złącza na podstawie wyłącznie parametrów kleju, podłoża i konstrukcji złącza. Lepkość kleju wskazuje, jak łatwo można pompować lub rozprowadzać produkt na powierzchni. Ujawnia informacje, wraz z szybkością wiązania i napięciem powierzchniowym, które są związane z właściwościami zwilżającymi kleju oraz informacje dotyczące wieku i składu kleju. Pomiary lepkości sypkich klejów lub uszczelniaczy są zwykle oparte na jednej z następujących metod opisanych w ASTM D 1084. Testy klejów i uszczelniaczy są przeprowadzane z różnych powodów. Służą do:
- Wybierz spośród materiałów lub procesów, takich jak klej, przyklejanie lub projektowanie połączeń;
- Monitorować jakość materiałów produkcyjnych, aby upewnić się, że nie uległy one zmianie od ostatniej weryfikacji, czy zostały użyte w procesie wiązania;
- Potwierdź skuteczność procesu wiązania, takiego jak czyszczenie powierzchni lub utwardzanie; lub
- Zbadaj parametry lub zmienne procesowe, które mogą prowadzić do zmierzonych różnic w wydajności wiązania
Istnieją dwie ogólne kategorie testów klejów i uszczelniaczy: podstawowe testy właściwości i testy końcowego zastosowania. Zasadnicze testy właściwości, takie jak badanie lepkości, są zwykle stosowane do oceny konsystencji przychodzącego kleju lub podłoża po zweryfikowaniu, czy system połączeń jest odpowiedni w konkretnym zastosowaniu. Często przeprowadza się podstawowe badania właściwości po wystąpieniu awarii lub niewyjaśnionego zdarzenia w celu ustalenia, czy zmiana w przychodzącym materiale mogła być potencjalnym winowajcą. Amerykańskie Towarzystwo Badań i Materiałów (ASTM) oraz inne organizacje zawodowe, takie jak Departament Obrony USA i Society of Automotive Engineers, określiły szereg standardowych testów klejów i uszczelniaczy.
Kontrola jakości przychodzących materiałów: Konieczne może być również przetestowanie przychodzącego produktu luzem pod kątem podstawowych właściwości. Kontrole te zwykle polegają na ocenie właściwości fizycznych i chemicznych, takich jak: kolor, lepkość, procent ciał stałych, waga na galon, czas przydatności do użycia, czas otwarty i przepływ. Niezwykle wysoki odsetek wad można przypisać słabemu wykonaniu lub niezrozumieniu przyczepności. Specyfikacje są niezbędną częścią programu kontroli jakości. Specyfikacja jest po prostu stwierdzeniem wymagań, które klej, szczeliwo lub proces muszą spełniać, aby zostać dopuszczonym do użycia.
Kleje mogą być jednoskładnikowe, ale często składają się z dwóch składników, żywicy i utwardzacza. Wszystkie składniki osobno i zmieszany produkt należy zbadać pod względem lepkości. Niektóre standardowe testy charakteryzujące podstawowe właściwości materiałów klejów i uszczelniaczy są następujące:
- ASTM D1084 Lepkość klejów
- ASTM D2556 Lepkość pozorna kleju o właściwościach przepływu zależnych od prędkości ścinania
- ASTM D3236 Lepkość klejów topliwych i materiałów powłokowych
Zarządzanie lepkością w systemach dostarczania
Te nowe kleje przemysłowe, stosowane zarówno do celów motoryzacyjnych, jak i do ogólnych celów produkcyjnych, są nakładane przy użyciu wielu różnych systemów dostarczania kleju. Obejmują one w pełni zrobotyzowane systemy aplikacji - które szybko nakładają precyzyjną, konsekwentnie odmierzoną kroplę kleju na obrabiany przedmiot, taki jak niezagruntowany panel nadwozia lub przednia szyba - po systemy aplikatorów pistoletowych używane przez pracowników zakładu do ręcznego nakładania kleju na panele i części podczas montażu linii produkcyjnej. Aby uzyskać bardziej równomierny przepływ i ścieg materiału podczas aplikacji, za pompą można dodać regulatory lepkości cieczy.
Reologia i lepkość to jedne z najważniejszych cech związanych ze szczeliwami i klejami, które powinny wykazywać właściwości podobne do cieczy (powinny płynąć), aby można je było zastosować, ale muszą mieć również wystarczającą `` przyczepność '', aby przylegać do lub wiązać podłoża razem - zachowanie, jest pod wpływem właściwości lepkosprężystych. Po nałożeniu większość materiałów jest następnie projektowana tak, aby przechodziła przemiana ciecz-ciało stałe w celu utworzenia solidnego uszczelnienia lub połączenia klejowego. W przypadku klejów o niskiej lepkości lepkość jest ważna dla penetracji powierzchni klejenia i wpływania do szczeliny klejowej. W przypadku klejów o wysokiej lepkości wymagana jest odpowiednia lepkość, aby wypełnić większe szczeliny i zapobiec przedostawaniu się kleju do małych szczelin i porów na powierzchni.
Lepkość jest pomiarem charakterystyk płynięcia, a jej kontrola jest jedną z najważniejszych operacji etapów dostarczania kleju i szczeliwa. Kluczowe punkty na temat tego, jak ważna jest lepkość gnojowicy:
- Poprzez pomiar lepkości można zauważyć zmiany gęstości, stabilności, zawartości rozpuszczalnika i masy cząsteczkowej. Lepkość jest skutecznym wskaźnikiem Rozkład wielkości cząstek. Zmiany rozkładu wielkości cząstek mogą wpływać na właściwości, w tym gęstość, reologię i grubość powłoki. Właściwości, na które mogą mieć wpływ odporność chemiczna, właściwości termiczne, odporność na uderzenia, skurcz, elastyczność, użyteczność i wytrzymałość. Ciągły monitoring lepkościoring i dokonanie wymaganych dostosowań do receptury jest niezbędne w celu uzyskania właściwych właściwości klejów i uszczelniaczy w odpowiednich zastosowaniach.
- Ciągły monitoring lepkościoring i kontrola są niezbędne, aby wykryć i uniknąć problemów w dostawie wynikających z czynników środowiskowych – temperatura, poziom wilgoci, dwutlenek węgla, pH i tlen, a także inne chemikalia mogą mieć niekorzystny wpływ na kleje i uszczelniacze.
W celu zapewnienia jednolitego procesu nanoszenia, aby nie marnować materiałów i zoptymalizować zużycie energii, wysoce pożądane jest automatyczne regulowanie lepkości do zasadniczo stałej wartości. Monitorowanie lepkości w czasie rzeczywistymoring I kontrola jest niezbędny do poprawić wydajność i obniżyć koszty w prawie każdym procesie formułowania i dostawy klejów i uszczelniaczy. Operatorzy procesów zdają sobie sprawę z potrzeby lepkościomierza, który monitoruje lepkość i temperaturę, i mogą wykorzystywać lepkość z kompensacją temperatury jako kluczową zmienną procesową, aby zapewnić spójność i zmniejszyć awarie.
Dlaczego monitor lepkościoring i kontrola mają kluczowe znaczenie przy formułowaniu, testowaniu i dostawie klejów i uszczelniaczy?
Szerokie i znaczące korzyści płynące z zarządzania lepkością podczas przygotowywania, testowania i aplikacji klejów i uszczelniaczy:
- Jakość przyczepności i uszczelnienia: Połączone części muszą być zgodne ze specyfikacjami gotowego produktu, a kontrola procesu ma kluczowe znaczenie, aby to osiągnąć. Monitor lepkości w liniioring i kontrola mogą pomóc w osiągnięciu wymaganej konsystencji w systemach dostarczania i formułowania klejów i uszczelniaczy.
- Zmniejszyć wady: Kontrola lepkości może pomóc złagodzić częstotliwość błędów w procesach przygotowania, testowania i dostarczania klejów i uszczelniaczy - uwięzienie powietrza, zwiększony poziom wilgoci
- Lepsza wydajność: Zapewnienie spójności w całym procesie powlekania znacznie zmniejsza wskaźniki odrzucania, oszczędzając koszty i czas oraz pomaga w ciągłych procesach dostawy. Techniki pomiaru offline są żmudne i niewiarygodne oraz wiążą się z dużymi opóźnieniami w procesie produkcyjnym, a ponadto wiążą się z wysokimi kosztami personelu przy próbkowaniu i przeprowadzaniu testów.
- Prawidłowe właściwości: Niska jakość mieszanki może negatywnie wpłynąć na pożądane właściwości połączeń - odporność na cykliczne zmiany temperatury, odporność chemiczną, izolację elektryczną, elastyczność, stabilność wymiarową, niski skurcz. Wszystkie te właściwości zależą od tego, jak dobrze kontrolowane są procesy, dlatego kontrola lepkości ma kluczowe znaczenie.
- Wydajne procesy: Automatyzacja pomiaru lepkości i kontrola w procesach odlewania inwestycji może pomóc producentom skrócić czas realizacji, zwiększyć wykorzystanie mocy i zoptymalizować wydajność.
- Koszty: Nieprawidłowa lepkość szkodzi nie tylko jakości. Niewłaściwe zarządzanie lepkościami zwiększa zużycie zagęszczaczy, wypełniaczy i rozcieńczalników, co wpływa na marże. Ciągłe pomiary lepkości podczas procesu mieszania mogą zapewnić jednorodność, zoptymalizować zużycie energii i zmniejszyć zużycie rozcieńczalników.
- Marnotrawstwo: Materiały odrzucone z powodu złej jakości można zmniejszyć przy odpowiednim zarządzaniu lepkością.
- Wydajność: Wyeliminowanie ręcznej kontroli lepkości zwalnia czas operatorów i pozwala im skupić się na innych zadaniach.
- Przyjazna dla środowiska: Zmniejszenie zużycia pigmentu i rozpuszczalnika jest korzystne dla środowiska.
- Zgodność z przepisami: Globalne i krajowe przepisy określają ogólne właściwości uszczelnień i klejów. Niezastosowanie się do tego ze względu na zmienność produkcji może prowadzić do znacznych szkód i strat klientów, oprócz zobowiązań wynikających z wadliwego wykonania w procesie produkcyjnym.
Aby zapewnić stałą, wysoką jakość i wolne od defektów nakładanie klejów i uszczelniaczy, zmiany lepkości w całym strumieniu procesu są monitorowane w czasie rzeczywistym, dokonując pomiarów od wartości bazowych, a nie tylko mierząc wartości bezwzględne, i dostosowując lepkość poprzez regulację składników mieszaniny i kompensację temperatury w celu utrzymania procesów w określonych granicach. Z ciągłym monitorowaniem lepkości onlineoringmożna skuteczniej kontrolować przygotowanie i dostawę, co znacznie poprawia właściwości metalurgiczne produktu końcowego.
Wyzwania procesowe
Operatorzy na rynku klejów i uszczelniaczy zdają sobie sprawę z potrzeby monitorowania lepkości, ale dokonywanie pomiarów poza laboratorium przez lata stanowiło wyzwanie dla inżynierów procesowych i działów jakości. Istniejące wiskozymetry laboratoryjne mają niewielką wartość w środowiskach procesowych, ponieważ na lepkość bezpośrednio wpływa temperatura, szybkość ścinania i inne zmienne, które są bardzo różne w trybie off-line od tych, które są w linii. Konwencjonalne metody kontrolowania lepkości preparatów okazały się nieodpowiednie nawet w zastosowaniach, w których dozwolone są duże wahania lepkości.
Tradycyjnie operatorzy mierzyli lepkość zawiesiny za pomocą kubka przepływowego Zahn. Pomiar podaje się jako czas, jaki upłynął, zanim objętość kubka przepłynęła przez otwór w dnie kubka. Punkt końcowy testu musi być wybrany tak, aby był spójny między testami. Procedura jest uciążliwa i czasochłonna. Jest niedokładny, niespójny i niepowtarzalny nawet w przypadku doświadczonego operatora. W procesie ciągłego odlewania próbkowanie interwałowe powoduje nadmierne opóźnienia. Lepkości nie można regulować w czasie rzeczywistym. Poza tym różne pojemniki zawierające preparat są otwarte; z powodu zmian temperatury otoczenia, wilgotności i innych czynników, takich jak temperatura, suchy klimat, rozpuszczalniki mogą być lotne, więc technika pomiaru lepkości na podstawie kubka staje się nieskuteczna.
Niektóre firmy stosują systemy zarządzania temperaturą, aby utrzymać punkt aplikacji w określonej optymalnej temperaturze w celu uzyskania stałej lepkości atramentu. Ale temperatura nie jest jedynym czynnikiem wpływającym na lepkość. Szybkość ścinania, warunki przepływu, ciśnienie i inne zmienne mogą również wpływać na zmiany lepkości. Systemy z kontrolowaną temperaturą mają również długi czas instalacji i dużą powierzchnię.
Konwencjonalne wiskozymetry wibracyjne są niezrównoważone i wymagają dużych mas, aby uniknąć dużego wpływu sił montażowych.
Rheonics' Rozwiązania
Zautomatyzowany pomiar i kontrola lepkości w linii ma kluczowe znaczenie dla kontrolowania lepkości receptury i aplikacji. Rheonics oferuje następujące rozwiązania oparte na zrównoważonym rezonatorze skrętnym do kontroli i optymalizacji procesu powlekania:
- Coaching Lepkość pomiary: Rheonics" SRV jest szerokopasmowym, wbudowanym urządzeniem do pomiaru lepkości z wbudowanym pomiarem temperatury płynu i jest w stanie wykrywać zmiany lepkości w dowolnym strumieniu procesu w czasie rzeczywistym.
- Coaching Lepkość i gęstość pomiary: Rheonics" SRD jest liniowym przyrządem do pomiaru gęstości i lepkości z wbudowanym pomiarem temperatury płynu. Jeśli pomiar gęstości jest ważny dla twoich operacji, SRD jest najlepszym czujnikiem, który zaspokoi twoje potrzeby, z możliwościami operacyjnymi podobnymi do SRV wraz z dokładnymi pomiarami gęstości.
Czujniki są hermetycznie zamknięte, dzięki czemu na ich działanie nie mają wpływu turbulencje i niejednorodność płynu. Zautomatyzowany pomiar lepkości online za pomocą SRV lub SRD eliminuje różnice w pobieraniu próbek i technikach laboratoryjnych. Czujnik jest instalowany albo w wiadrze do powlekania, albo w przewodzie, przez który powłoka jest pompowana do aplikatora, w sposób ciągły mierząc formułowaną lepkość układu (i gęstość w przypadku SRD). Spójność aplikacji jest osiągana dzięki automatyzacji systemu dozowania poprzez sterownik procesu oparty na pomiarach lepkości i temperatury w czasie rzeczywistym. Zastosowanie SRV / SRD w linii procesu powlekania poprawia wydajność transferu, poprawiając produktywność, marże zysku i cele środowiskowe / regulacyjne. Czujniki mają kompaktową obudowę, umożliwiającą prostą instalację OEM i modernizację. Nie wymagają konserwacji ani ponownej konfiguracji. Czujniki zapewniają dokładne, powtarzalne wyniki bez względu na to, jak i gdzie są zamontowane, bez potrzeby stosowania specjalnych komór, gumowych uszczelek lub ochrony mechanicznej. Bez materiałów eksploatacyjnych SRV i SRD są niezwykle łatwe w obsłudze i nie wymagają konserwacji.
Rheonics' Korzyść
Kompaktowy kształt, brak ruchomych części i nie wymaga konserwacji
Rheonics' SRV i SRD mają bardzo małe wymiary, co ułatwia instalację OEM i modernizację. Umożliwiają łatwą integrację z dowolnym strumieniem procesu. Są łatwe w czyszczeniu i nie wymagają konserwacji ani ponownej konfiguracji. Mają niewielką powierzchnię, co umożliwia instalację Inline w liniach atramentowych, co pozwala uniknąć dodatkowej przestrzeni lub wymagań dotyczących adapterów w prasie i wózkach z atramentem.
Wysoka stabilność i niewrażliwość na warunki montażu: Możliwa dowolna konfiguracja
Rheonics SRV i SRD wykorzystują unikalny, opatentowany rezonator współosiowy, w którym dwa końce czujników skręcają się w przeciwnych kierunkach, eliminując momenty reakcji podczas ich montażu, a tym samym czyniąc je całkowicie niewrażliwymi na warunki montażu i natężenie przepływu atramentu. Czujniki te z łatwością radzą sobie z regularną przeprowadzką. Element czujnika znajduje się bezpośrednio w płynie, bez konieczności stosowania specjalnej obudowy lub klatki ochronnej.
Łatwa instalacja i brak konieczności ponownej konfiguracji / ponownej kalibracji
Wymień czujniki bez wymiany lub przeprogramowania elektroniki, doraźne wymiany zarówno czujnika, jak i elektroniki, bez aktualizacji oprogramowania sprzętowego lub zmian współczynnika kalibracji. Łatwy montaż. Wkręca się w gwint ¾” NPT w złączce przewodu atramentowego. Żadnych komór, O-ring uszczelki lub uszczelki. Łatwe do usunięcia w celu czyszczenia lub kontroli. SRV dostępny z kołnierzem i tri-clamp złącze ułatwiające montaż i demontaż.
Niskie zużycie energii
Zasilacz 24 V DC o poborze prądu mniejszym niż 0.1 A podczas normalnej pracy
Krótki czas reakcji i lepkość kompensowana temperaturą
Ultraszybka i solidna elektronika w połączeniu z kompleksowymi modelami obliczeniowymi sprawia, że Rheonics urządzenia jedne z najszybszych i najdokładniejszych w branży. SRV i SRD umożliwiają dokładne pomiary lepkości (i gęstości w przypadku SRD) w czasie rzeczywistym co sekundę i nie mają na nie wpływu zmiany natężenia przepływu!
Szerokie możliwości operacyjne
RheonicsPrzyrządy są zbudowane tak, aby wykonywać pomiary w najtrudniejszych warunkach. SRV ma najszerszy zakres operacyjny na rynku wiskozymetrów procesowych inline:
- Zakres ciśnienia do 5000 psi
- Zakres temperatur od -40 do 200 ° C
- Zakres lepkości: 0.5 cP do 50,000 XNUMX cP
SRD: Pojedynczy instrument, potrójna funkcja - Lepkość, temperatura i gęstość
Rheonics" SRD to wyjątkowy produkt, który zastępuje trzy różne przyrządy do pomiaru lepkości, gęstości i temperatury. Eliminuje trudności związane ze wspólną lokalizacją trzech różnych instrumentów i zapewnia niezwykle dokładne i powtarzalne pomiary w najtrudniejszych warunkach.
Uzyskaj odpowiednią jakość druku, obniż koszty i zwiększ produktywność
Zintegruj SRV / SRD z linią technologiczną i zapewnij spójność kolorów podczas całego procesu drukowania. Osiągaj stałe kolory bez obawy o różnice kolorystyczne. SRV (i SRD) stale monitoruje i kontroluje lepkość (i gęstość w przypadku SRD) i zapobiega nadmiernemu zużyciu drogich pigmentów i rozpuszczalników. Niezawodne i automatyczne podawanie atramentu zapewnia, że prasy pracują szybciej i oszczędzają czas operatora. Zoptymalizuj proces drukowania za pomocą SRV i doświadcz mniejszej liczby odrzutów, mniej odpadów, mniej skarg klientów, mniej przestojów w prasie i oszczędność kosztów materiałów. A na koniec przyczynia się do lepszego wyniku i lepszego środowiska!
Czyszczenie na miejscu (CIP)
SRV (i SRD) monitoruje czyszczenie linii atramentu przez monitoring lepkość (i gęstość) rozpuszczalnika podczas fazy czyszczenia. Czujnik wykrywa wszelkie drobne pozostałości, umożliwiając operatorowi podjęcie decyzji, kiedy linia jest celowo czysta. Alternatywnie SRV dostarcza informacje do automatycznego systemu czyszczenia, aby zapewnić pełne i powtarzalne czyszczenie pomiędzy cyklami.
Doskonała konstrukcja i technologia czujnika
Zaawansowana, opatentowana elektronika trzeciej generacji steruje tymi czujnikami i ocenia ich reakcję. SRV i SRD są dostępne ze standardowymi przyłączami procesowymi, takimi jak ¾” NPT i 3” Tri-clamp umożliwiając operatorom wymianę istniejącego czujnika temperatury w linii technologicznej na SRV/SRD, dostarczając bardzo cennych i przydatnych informacji o płynie procesowym, takich jak lepkość, oprócz dokładnego pomiaru temperatury za pomocą wbudowanego czujnika Pt1000 (dostępna klasa AA, A, B DIN EN 60751) .
Elektronika zbudowana tak, aby pasowała do Twoich potrzeb
Dostępne w obudowie przetwornika w wykonaniu przeciwwybuchowym i niewielkim obudowie na szynę DIN, elektronika czujnika umożliwia łatwą integrację z rurociągami procesowymi i wewnątrz szaf urządzeń.
Łatwa integracja
Wiele analogowych i cyfrowych metod komunikacji zaimplementowanych w elektronice czujnika sprawia, że podłączenie do przemysłowych sterowników PLC i systemów sterowania jest proste i proste.
Zgodność z ATEX i IECEx
Rheonics oferuje czujniki iskrobezpieczne z certyfikatami ATEX i IECEx do stosowania w środowiskach niebezpiecznych. Czujniki te spełniają zasadnicze wymagania bezpieczeństwa i higieny pracy związane z projektowaniem i konstrukcją urządzeń i systemów ochronnych przeznaczonych do stosowania w przestrzeniach zagrożonych wybuchem.
Posiadane przez firmę certyfikaty iskrobezpieczności i przeciwwybuchowości Rheonics pozwala także na dostosowanie istniejącego czujnika, pozwalając naszym klientom uniknąć czasu i kosztów związanych z identyfikacją i testowaniem alternatywy. Można dostarczyć czujniki niestandardowe do zastosowań wymagających od jednej jednostki do tysięcy jednostek; z czasem realizacji wynoszącym tygodnie zamiast miesięcy.
Rheonics SRV & SRD posiadają zarówno certyfikat ATEX, jak i IECEx.
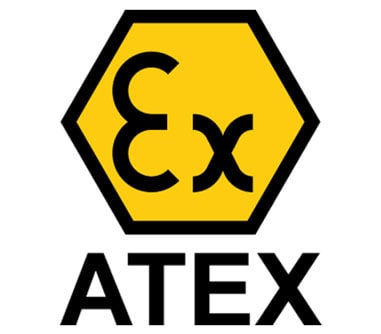
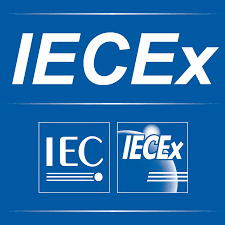
Realizacja
Zainstaluj czujnik bezpośrednio w strumieniu procesowym, aby wykonywać pomiary lepkości i gęstości w czasie rzeczywistym. Nie jest wymagana linia obejściowa: czujnik może być zanurzony w linii, szybkość przepływu i wibracje nie wpływają na stabilność i dokładność pomiaru. Zoptymalizuj wydajność mieszania, zapewniając powtarzalne, kolejne i spójne testy płynu.
Rheonics Wybór instrumentu
Rheonics projektuje, produkuje i sprzedaje innowacyjne czujniki i monitory płynóworing systemy. Precyzja zbudowana w Szwajcarii, RheonicsWiskozymetry in-line charakteryzują się czułością wymaganą w danym zastosowaniu i niezawodnością niezbędną do przetrwania w trudnych warunkach pracy. Stabilne wyniki – nawet w niekorzystnych warunkach przepływu. Brak wpływu spadku ciśnienia lub natężenia przepływu. Równie dobrze nadaje się do pomiarów kontroli jakości w laboratorium.
Sugerowane produkty do zastosowania
- Szeroki zakres lepkości - monitoruj cały proces
- Powtarzalne pomiary zarówno płynów newtonowskich, jak i nienewtonowskich, płynów jednofazowych i wielofazowych
- Hermetycznie zamknięte, wszystkie części ze stali nierdzewnej 316L zwilżane
- Wbudowany pomiar temperatury płynu
- Kompaktowy kształt ułatwiający instalację w istniejących liniach technologicznych
- Łatwy w czyszczeniu, nie wymaga konserwacji ani ponownej konfiguracji
- Pojedynczy przyrząd do pomiaru gęstości procesowej, lepkości i temperatury
- Powtarzalne pomiary zarówno płynów newtonowskich, jak i nienewtonowskich, płynów jednofazowych i wielofazowych
- Konstrukcja wykonana w całości z metalu (stal nierdzewna 316L)
- Wbudowany pomiar temperatury płynu
- Kompaktowy kształt ułatwiający montaż w istniejących rurach
- Łatwy w czyszczeniu, nie wymaga konserwacji ani ponownej konfiguracji