Wprowadzenie
Polimery stały się tanimi substytutami produktów naturalnych, oferując wysokiej jakości opcje do różnych zastosowań przemysłowych ze względu na ich niski koszt, zakres właściwości (wysoka odporność chemiczna, odporność na wysoką temperaturę, wysoki stosunek wytrzymałości do masy) i łatwość przetwarzania. Stosuje się je jako folie do formowania stałych formowanych części do karoserii samochodowych, szafek telewizyjnych, części lotniczych, pianek do filiżanek kawy i izolacji lodówki, włókien do odzieży i dywanów, klejów, gumy do opon i dętek, farb i innych powłok oraz wielu innych inne aplikacje.
Wytłaczanie polimerów jest niezwykle energochłonne, a monitorowanie odbywa się w czasie rzeczywistymoring zużycia energii i jakości stopu stało się niezwykle konieczne, aby spełnić nowe przepisy dotyczące emisji dwutlenku węgla i przetrwać na wysoce konkurencyjnym rynku tworzyw sztucznych.
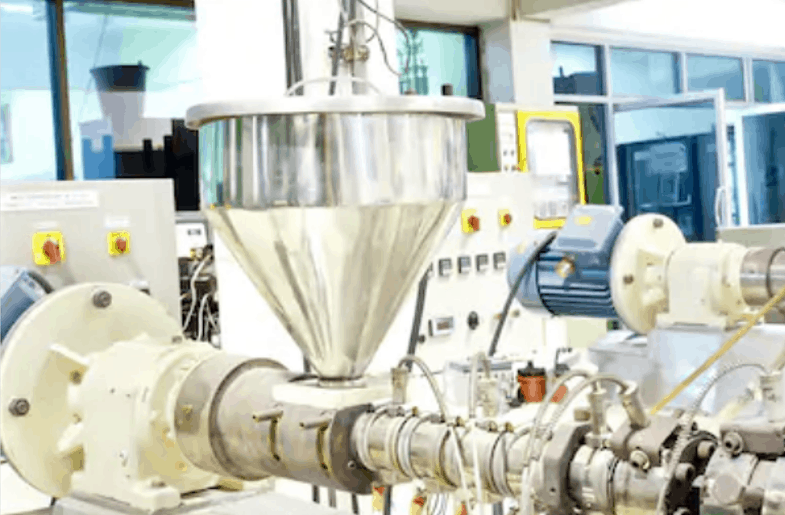
Zastosowanie
Polimery poddawane są formowaniu wtryskowemu, formowaniu tłocznemu lub wytłaczaniu - z których wszystkie wymagają wymuszenia kształtu polimeru. Przetwarzanie jest jednak energochłonne. W Wielkiej Brytanii koszty energii elektrycznej do przetwórstwa tworzyw sztucznych wynoszą około 350 milionów funtów rocznie. Zmniejszenie zużycia energii elektrycznej przyniosłoby ogromne oszczędności i znaczne zmniejszenie obciążenia środowiska.
Energię zużywaną podczas przetwarzania polimeru można podzielić na dwa aspekty: system zarządzania energią wysokiego poziomu i sterowanie maszynami niskiego poziomu. W przypadku systemu zarządzania energią wysokiego poziomu można zmniejszyć zużycie energii o około 30% dzięki zarządzaniu procesami i konserwacji. Bez odpowiedniego zarządzania procesem nieoptymalne ustawienia robocze, takie jak ogrzewanie termiczne, chłodzenie i prędkość przetwarzania w przypadku procesu wytłaczania polimerów, przyczyniają się do ogromnego marnotrawstwa energii.
Gęstość i lepkość stopionych polimerów są bardzo ważnymi parametrami fizykochemicznymi w procesie wytwarzania polimeru. Są to bardzo znaczące czynniki wpływające na koszt produkcji i rentowność procesu produkcyjnego. Polimery poddawane są formowaniu wtryskowemu, formowaniu tłocznemu lub wytłaczaniu - z których wszystkie wymagają wymuszenia kształtu polimeru.
Charakterystyka materiałów w linii pokazuje rosnącą popularność wśród naukowców pracujących nad poprawą wydajności wielu istniejących procesów produkcyjnych, a także nowych procesów. Korzyści związane z zastosowaniem tych technik mogą być bezpośrednio związane z poprawą jakości i obniżeniem kosztów produkcji. Pomiary reologii mogą być wykorzystane do charakterystyki materiału, określenia przetwarzalności oraz jako dane wejściowe do symulacji komputerowych. Reologia ma przewagę nad innymi metodami ze względu na jej wrażliwość na niektóre aspekty struktury, takie jak ogon o wysokiej masie cząsteczkowej i rozgałęzienie. W wielu przypadkach charakterystyka reologiczna jest znacznie szybsza niż jej odpowiedniki.
W procesie wytłaczania gęstość produktu jest najbardziej krytycznym czynnikiem wpływającym na koszty produkcji i ogólną rentowność procesu produkcyjnego. Zmniejszenie gęstości zmniejsza koszty surowców. Jeśli jednak gęstość produktu jest utrzymywana na zbyt niskim poziomie, pogarsza to właściwości mechaniczne i dokładność geometryczną. Dlatego niezbędna jest równowaga krytyczna w celu obniżenia kosztów materiałów przy jednoczesnym zachowaniu odpowiedniej wytrzymałości i dokładności. Gęstość pianki PVC można kontrolować, zmieniając rodzaj i ilość dodatków złożonych, parametry przetwarzania (temperatura, prędkość ślimaka) lub jedno i drugie.
Głównym celem ciągłego dostosowywania ustawień roboczych jest zagwarantowanie stałej jakości stopu. Badania wykazały, że lepkość stopu jest prawdopodobnie najlepszym wskaźnikiem jakości stopu (Cogswell, 1981). W przypadku materiałów bardziej lepkich należy zastosować większą siłę i dostosować inne warunki, np. temperaturę. Producenci muszą dokładnie zrozumieć te informacje, aby zapewnić odpowiednie warunki i najlepsze wykorzystanie zasobów. W celu optymalizacji ustawień operacyjnych monitor w czasie rzeczywistymoring wymagana jest lepkość stopu.
Wyzwania
Wytłaczanie jedno- i dwuślimakowe to najczęściej stosowane techniki wytłaczania. Granulki z tworzywa sztucznego są przepychane przez śrubę przemieszczającą się ze strefy zasilania do matrycy, a granulki topią się pod wpływem ciepła od naprężenia ścinającego i ogrzewania beczki.
Związane z aplikacją
Większość materiałów polimerowych wykazuje wyjątkowo skomplikowane zachowanie, szczególnie w przypadku stopionych polimerów. Aplikacja wymaga pomiarów w bardzo trudnych warunkach - pod wysokim ciśnieniem (50-100 MPa) i wysoką temperaturą (około 150-300 ° C). W HPHT istnieje wysokie ryzyko problemów z dokładnością i niezawodnością.
Problemy z monitorowaniem procesuoring z poborem mocy silnika
Niewiele firm zajmujących się przetwórstwem tworzyw sztucznych monitoruje zużycie energii przez silnik wytłaczarki, aby zbadać stabilność stopu, jakość produktu końcowego, a także efektywność energetyczną. Jednak z tą techniką jest kilka wyzwań:
- Instalacja liczników mocy dla każdej wytłaczarki jest droga, a modele matematyczne oparte na ustawieniach procesu mogą być lepszą alternatywą
- Istniejące modele są w dużym stopniu zależne od geometrii wytłaczarki i materiałów polimerowych, trudno jest używać tego samego modelu w różnych przypadkach użycia bez ponownego szkolenia
Problemy z monitorowaniem procesuoring z ciśnieniem stopu
W przemyśle ciśnienie stopu w pobliżu końcówki śruby jest zwykle akceptowane jako główny wskaźnik jakości stopu. Kilka ograniczeń dzięki tej technice:
- Wiadomo, że ciśnienie jest proporcjonalne do prędkości ślimaka, jednak nieznacznie wpływa na to również temperatura stopu, geometria ślimaka i przetwarzany materiał polimerowy.
- Niestabilne ciśnienie stopu powoduje wahania wydajności i zmiany jakości produktu końcowego.
Ograniczenia tradycyjnych technik pomiaru lepkości
Reologiczne zachowanie większości materiałów polimerowych jest dość złożone. Lepkość zależy zarówno od ścinania, jak i od historii termicznej. Często lepkość polimeru mierzy się w trybie off-line. Próbkę związku polimerowego topi się i umieszcza w specjalnej rurce kapilarnej (szklany lepkościomierz) lub przez włączenie rurki kapilarnej zamontowanej równolegle do wytłaczarki w przypadku pomiarów online. Obie techniki wiążą się z długimi opóźnieniami wynikającymi z czasu potrzebnego do przepłynięcia stopu przez linie przesyłowe i kapilarę. W niektórych przypadkach wiskozymetry są montowane na liniach wytłaczających, które mierzą naprężenie na ściance matrycy, mierząc spadek ciśnienia wzdłuż szczeliny lub kapilary, a szybkość przepływu mierzy się za pomocą dodatkowego miernika przepływu. Chociaż metody te dają pomiary lepkości bardziej odpowiednie dla procesu wytłaczania, przepływomierz często zaburza strumień stopu, zmieniając w ten sposób pierwotne właściwości przepływu.
Konwencjonalne wiskozymetry mechaniczne i elektromechaniczne przeznaczone głównie do pomiarów laboratoryjnych są trudne do zintegrowania z systemem sterowania i monitorowaniaoring środowisko. Obecna metodologia testów w laboratoriach zewnętrznych nie jest optymalna i kosztowna ze względu na wyzwania logistyczne związane z wysyłką i wysokie koszty stałe. Złożonych zmian zachodzących wewnątrz silnika lub sprężarki często nie można określić na podstawie rutynowej próbki oleju, ponieważ dane reprezentowane przez taką próbkę po prostu odzwierciedlają migawkowy stan oleju w momencie pobrania próbki, a na konwencjonalne oprzyrządowanie może wpływać szybkość ścinania, temperatura i inne zmienne.
Dlaczego pomiar reologii online w czasie rzeczywistym jest ważny?
Istnieje kilka motywacyjnych korzyści z perspektywy kosztów, środowiska i logistyki, a monitorowanie lepkości on-line w czasie rzeczywistymoring w procesie produkcji polimerów. Jest to doskonałe narzędzie do charakteryzowania materiałów i rozwiązywania różnych problemów. Najważniejsze korzyści są następujące:
Korzyści ekonomiczne i logistyczne, niższe koszty produkcji: Analiza lepkości on-line zmniejszyłaby liczbę próbek wysyłanych do laboratoriów zewnętrznych i związane z tym koszty. Ciągłe wyniki analiz przeprowadzanych na miejscu zmniejszyłyby również koszty pracy / koszty wysyłki i błąd pobierania próbek.
Pomiary reologii mogą pomóc rozwiązać problemy podczas przetwarzania polimerów i zmniejszyć liczbę błędów:
- Skóra rekina: Materiały, które nie są zbyt cienkie przy ścinaniu, są podatne na skórę rekina przy stosunkowo niższych wydajnościach. Informacje o lepkości materiału w temperaturze przetwarzania (w obszarze wargi) mogą być niezbędne do zmniejszenia naprężeń ścinających, zwiększenia temperatury matrycy lub zastosowania dodatków, które sprzyjają poślizgowi i zapobiegają defektom.
- Niestabilność pęcherzyków podczas rozdmuchiwania filmu: Niska wytrzymałość stopu materiału może powodować tę wadę. Wartości lepkości i / lub wytrzymałości stopu materiałów mogą być użyte do porównania stabilności pęcherzyków różnych materiałów i wyboru odpowiedniego materiału do zastosowania. Chłodzenie może pomóc obniżyć temperaturę pęcherzyków, a tym samym zwiększyć wytrzymałość stopu.
- Niewłaściwe mieszanie dwóch polimerów: Gdy różnica lepkości między dwoma mieszanymi polimerami jest duża (np. Ponad 5 razy), mieszanie jest niezwykle trudne, ponieważ naprężenie ścinające wywierane przez matrycę na fazę rozproszoną o wyższej lepkości nie jest wystarczająco duże, aby spowodować rozpad. Działanie naprawcze polegałoby na zastosowaniu matrycy o wyższej lepkości.
Poprawiona jakość produktu końcowego: Pomiary reologiczne surowca i produktu końcowego mogą scharakteryzować właściwości produktu, takie jak odporność na uderzenia, optyka, wypaczenie, kruchość itp. Ciągły monitoringoring może pomóc wykryć wszelkie modyfikacje lub degradację, które mogą wystąpić podczas procesu wytłaczania.
Zmniejszone zużycie energii: W celu optymalizacji ustawień operacyjnych monitor w czasie rzeczywistymoring wymagana jest lepkość stopu. Optymalne wykorzystanie zasobów i energii elektrycznej w produkcji przy ścisłej kontroli procesów zapewniają pomiary reologiczne inline w czasie rzeczywistym.
Zwiększone bezpieczeństwo pracowników: Inne czynniki, takie jak wymagania w zakresie ochrony zdrowia i bezpieczeństwa przy pracy z rozpuszczalnikami, dbałość o środowisko oraz potrzeba specjalistycznego personelu do przeprowadzenia tych testów (które muszą być przeprowadzone w laboratorium) zwiększają popularność metody bezrozpuszczalnikowej.
Krótszy czas reakcji: Analiza lepkości (i gęstości) in situ zmniejszyłaby / wyeliminowała opóźnienie między pobraniem próbki a otrzymaniem odpowiedzi z laboratorium.
Środowisko: Wykorzystanie zasobów można zmaksymalizować poprzez monitorowanie on-lineoring systemów, co skutkuje zmniejszeniem ilości odpadów, co jest korzystne dla środowiska. Większy zrównoważony rozwój poprzez zmniejszoną emisję.
Rheonics' Rozwiązania
Zautomatyzowany pomiar lepkości na linii w czasie rzeczywistym ma kluczowe znaczenie w produkcji polimerów. Rheonics oferuje następujące rozwiązania oparte na zrównoważonym rezonatorze skrętnym do kontroli i optymalizacji procesu przetwórstwa polimerów:
- In-line Lepkość pomiary: Rheonics" SRV jest szerokopasmowym, wbudowanym urządzeniem do pomiaru lepkości z wbudowanym pomiarem temperatury płynu i jest w stanie wykrywać zmiany lepkości w dowolnym strumieniu procesu w czasie rzeczywistym.
- In-line Lepkość i gęstość pomiary: Rheonics" SRD jest równoległym przyrządem do pomiaru gęstości i lepkości z wbudowanym pomiarem temperatury płynu. Jeśli pomiar gęstości jest ważny dla twoich operacji, SRD jest najlepszym czujnikiem, który zaspokoi twoje potrzeby, z możliwościami operacyjnymi podobnymi do SRV wraz z dokładnymi pomiarami gęstości.
Zautomatyzowany pomiar lepkości na linii za pomocą SRV lub SRD eliminuje różnice w pobieraniu próbek i technikach laboratoryjnych, które są stosowane do pomiaru lepkości tradycyjnymi metodami. Czujnik umieszczony jest w linii, dzięki czemu w sposób ciągły mierzy lepkość (i gęstość w przypadku SRD). Używanie SRV/SRD do monitorowania procesuoring może poprawić produktywność i zwiększyć marże zysku. Oba czujniki mają kompaktową obudowę, co ułatwia instalację OEM i modernizację. Nie wymagają konserwacji ani ponownej konfiguracji. Obydwa czujniki zapewniają dokładne, powtarzalne wyniki niezależnie od sposobu i miejsca montażu, bez konieczności stosowania specjalnych komór, uszczelek gumowych czy zabezpieczeń mechanicznych. Nie wymagające materiałów eksploatacyjnych, SRV i SRD są niezwykle łatwe w obsłudze.
Kompaktowy kształt, brak ruchomych części i nie wymaga konserwacji
Rheonics' SRV i SRD mają bardzo małe wymiary, co ułatwia instalację OEM i modernizację. Umożliwiają łatwą integrację z dowolnym strumieniem procesu. Są łatwe w czyszczeniu i nie wymagają konserwacji ani ponownej konfiguracji. Mają niewielką powierzchnię, co pozwala na instalację Inline w dowolnej linii technologicznej, bez konieczności stosowania dodatkowej przestrzeni lub adaptera.
Wysoka stabilność i niewrażliwość na warunki montażu: Możliwa dowolna konfiguracja
Rheonics SRV i SRD wykorzystują unikalny, opatentowany rezonator współosiowy, w którym dwa końce czujników skręcają się w przeciwnych kierunkach, eliminując momenty reakcji podczas ich montażu, a tym samym czyniąc je całkowicie niewrażliwymi na warunki montażu i natężenia przepływu. Czujniki te z łatwością radzą sobie z regularną przeprowadzką. Element czujnika znajduje się bezpośrednio w płynie, bez konieczności stosowania specjalnej obudowy lub klatki ochronnej.
Natychmiastowe dokładne odczyty warunków procesu - Pełny przegląd systemu i sterowanie predykcyjne
RheonicsOprogramowanie jest potężne, intuicyjne i wygodne w obsłudze. Lepkość można monitorować w czasie rzeczywistym na komputerze. Zarządzanie wieloma czujnikami odbywa się z jednego pulpitu nawigacyjnego rozmieszczonego po całej hali produkcyjnej. Brak wpływu pulsacji ciśnienia podczas pompowania na działanie czujnika i dokładność pomiaru. Odporny na wstrząsy, wibracje i warunki przepływu.
Łatwa instalacja i brak konieczności ponownej konfiguracji / ponownej kalibracji
Wymień czujniki bez wymiany lub przeprogramowania elektroniki, doraźne wymiany zarówno czujnika, jak i elektroniki, bez aktualizacji oprogramowania sprzętowego lub zmian współczynnika kalibracji. Łatwy montaż. Wkręca się w gwint ¾” NPT w złączce przewodu atramentowego. Żadnych komór, O-ring uszczelki lub uszczelki. Łatwe do usunięcia w celu czyszczenia lub kontroli. SRV dostępny z kołnierzem i tri-clamp złącze ułatwiające montaż i demontaż.
Niskie zużycie energii
Zasilacz 24 V DC o poborze prądu mniejszym niż 0.1 A podczas normalnej pracy
Krótki czas reakcji i lepkość kompensowana temperaturą
Ultraszybka i solidna elektronika w połączeniu z kompleksowymi modelami obliczeniowymi sprawia, że Rheonics urządzenia jedne z najszybszych i najdokładniejszych w branży. SRV i SRD umożliwiają dokładne pomiary lepkości (i gęstości w przypadku SRD) w czasie rzeczywistym co sekundę i nie mają na nie wpływu zmiany natężenia przepływu!
Szerokie możliwości operacyjne
RheonicsPrzyrządy są zbudowane tak, aby wykonywać pomiary w najtrudniejszych warunkach. SRV ma najszerszy zakres operacyjny na rynku wiskozymetrów procesowych inline:
- Zakres ciśnienia do 5000 psi
- Zakres temperatur od -40 do 200 ° C
- Zakres lepkości: 0.5 cP do 50,000 XNUMX cP
SRD: Pojedynczy instrument, potrójna funkcja - Lepkość, temperatura i gęstość
Rheonics' SRD to unikalny produkt, który zastępuje trzy różne przyrządy do pomiarów lepkości, gęstości i temperatury. Eliminuje trudności związane ze zlokalizowaniem trzech różnych instrumentów i zapewnia niezwykle dokładne i powtarzalne pomiary w najtrudniejszych warunkach.
Czyszczenie na miejscu (CIP)
SRV (i SRD) monitoruje czyszczenie linii za pomocą monitaoring lepkość (i gęstość) rozpuszczalnika podczas fazy czyszczenia. Czujnik wykrywa wszelkie drobne pozostałości, umożliwiając operatorowi podjęcie decyzji, kiedy linia jest celowo czysta. Alternatywnie SRV dostarcza informacje do automatycznego systemu czyszczenia, aby zapewnić pełne i powtarzalne czyszczenie pomiędzy seriami, w przeciwieństwie do szklanych kapilar.
Doskonała konstrukcja i technologia czujnika
Zaawansowana, opatentowana elektronika trzeciej generacji steruje tymi czujnikami i ocenia ich reakcję. SRV i SRD są dostępne ze standardowymi przyłączami procesowymi, takimi jak ¾” NPT i 3” Tri-clamp umożliwiając operatorom wymianę istniejącego czujnika temperatury w linii technologicznej na SRV/SRD, dostarczając bardzo cennych i przydatnych informacji o płynie procesowym, takich jak lepkość, oprócz dokładnego pomiaru temperatury za pomocą wbudowanego czujnika Pt1000 (dostępna klasa AA, A, B DIN EN 60751) .
Elektronika zbudowana tak, aby pasowała do Twoich potrzeb
Dostępne w obudowie przetwornika w wykonaniu przeciwwybuchowym i niewielkim obudowie na szynę DIN, elektronika czujnika umożliwia łatwą integrację z rurociągami procesowymi i wewnątrz szaf urządzeń.
Łatwa integracja
Wiele analogowych i cyfrowych metod komunikacji zaimplementowanych w elektronice czujnika sprawia, że podłączenie do przemysłowych sterowników PLC i systemów sterowania jest proste i proste.
Zgodność z ATEX i IECEx
Rheonics oferuje czujniki iskrobezpieczne z certyfikatami ATEX i IECEx do stosowania w środowiskach niebezpiecznych. Czujniki te spełniają zasadnicze wymagania bezpieczeństwa i higieny pracy związane z projektowaniem i konstrukcją urządzeń i systemów ochronnych przeznaczonych do stosowania w przestrzeniach zagrożonych wybuchem.
Posiadane przez firmę certyfikaty iskrobezpieczności i przeciwwybuchowości Rheonics pozwala także na dostosowanie istniejącego czujnika, pozwalając naszym klientom uniknąć czasu i kosztów związanych z identyfikacją i testowaniem alternatywy. Można dostarczyć czujniki niestandardowe do zastosowań wymagających od jednej jednostki do tysięcy jednostek; z czasem realizacji wynoszącym tygodnie zamiast miesięcy.
Rheonics SRV & SRD posiadają zarówno certyfikat ATEX, jak i IECEx.
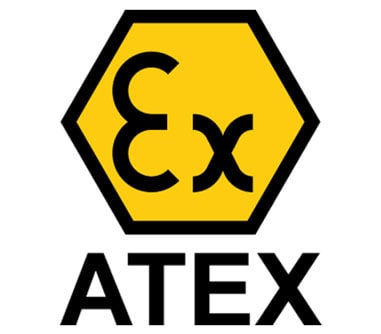
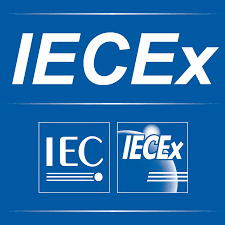
Realizacja
Zainstaluj czujnik bezpośrednio w strumieniu procesowym, aby wykonywać pomiary lepkości i gęstości w czasie rzeczywistym. Nie jest wymagana linia obejściowa: czujnik można zanurzyć w linii, szybkość przepływu i wibracje nie wpływają na stabilność i dokładność pomiaru. Zoptymalizuj proces decyzyjny, zapewniając powtarzalne, kolejne i spójne testy płynu.
Rheonics Wybór instrumentu
Rheonics projektuje, produkuje i sprzedaje innowacyjne czujniki i monitory płynóworing systemy. Precyzja zbudowana w Szwajcarii, RheonicsWiskozymetry in-line charakteryzują się czułością wymaganą w danym zastosowaniu i niezawodnością niezbędną do przetrwania w trudnych warunkach pracy. Stabilne wyniki – nawet w niekorzystnych warunkach przepływu. Brak wpływu spadku ciśnienia lub natężenia przepływu. Równie dobrze nadaje się do pomiarów kontroli jakości w laboratorium.
Sugerowane produkty do zastosowania
• Szeroki zakres lepkości - monitoruj cały proces
• Powtarzalne pomiary zarówno płynów newtonowskich, jak i nienewtonowskich, płynów jednofazowych i wielofazowych
• Konstrukcja wykonana w całości z metalu (stal nierdzewna 316L)
• Wbudowany pomiar temperatury płynu
• Kompaktowy kształt dla łatwej instalacji w istniejących liniach technologicznych
• Łatwy w czyszczeniu, nie wymaga konserwacji ani ponownej konfiguracji
• Pojedynczy przyrząd do pomiaru gęstości procesu, lepkości i temperatury
• Powtarzalne pomiary zarówno płynów newtonowskich, jak i nienewtonowskich, płynów jednofazowych i wielofazowych
• Konstrukcja wykonana w całości z metalu (stal nierdzewna 316L)
• Wbudowany pomiar temperatury płynu
• Kompaktowy kształt ułatwiający montaż w istniejących rurach
• Łatwy w czyszczeniu, nie wymaga konserwacji ani ponownej konfiguracji