Wprowadzenie
Wielkość globalnego rynku powłok do izolacji elektrycznej w 2015 r. Wyniosła 2 miliardy USD i oczekuje się, że w nadchodzących latach znacznie wzrośnie, głównie ze względu na rozwój sektora energetycznego (globalny rynek przesyłu i dystrybucji). Największe trendy na wschodzących rynkach, które sprzyjają rozwojowi, to rosnący przemysł energii słonecznej, rosnące inwestycje w inteligentną sieć energetyczną i stosowanie energooszczędnych silników. Główne obszary zastosowań to elektrotechnika i elektronika, motoryzacja, medycyna i lotnictwo.
Oczekuje się, że niestabilne koszty surowców i wysokie koszty preparatów będą stanowić poważne wyzwanie dla uczestników rynku. Surowe przepisy rządowe nałożone na rynek, szczególnie w Ameryce Północnej i Europie, ograniczają ilość LZO w produktach do powlekania. Zmusiło to producentów powłok do ekologizacji i przyjęcia zrównoważonego rozwoju jako celu, a także wnoszą wysokie inwestycje w badania i rozwój w celu opracowania innowacyjnych i nowych produktów, które mogą być oferowane przy niskich kosztach, przy jednoczesnym przestrzeganiu wytycznych regulacyjnych. Kluczowi uczestnicy branży na rynku elektrycznych powłok izolacyjnych nadal dążą do wysokiej integracji w całym łańcuchu wartości, ulepszeń procesów w celu uzyskania najwyższej jakości i redukcji kosztów w celu rozszerzenia swojego portfolio produktów.
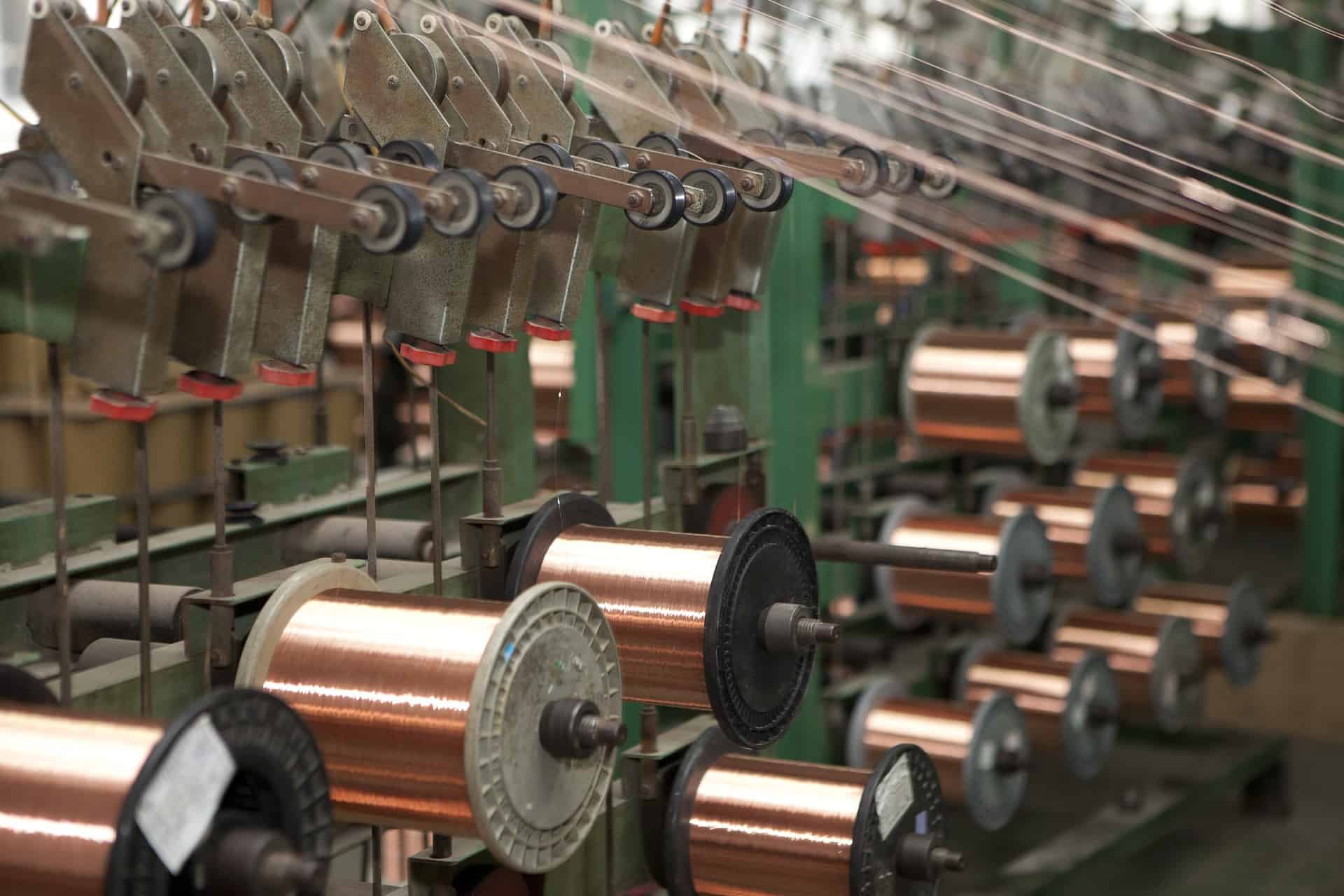
Zastosowanie
Druty miedziane i aluminiowe do produkcji transformatorów, silników elektrycznych, cewek indukcyjnych, generatorów, głośników, siłowników z głowicą dysku twardego, elektromagnesów i wielu innych zastosowań, są powlekane bardzo cienką, elektrycznie izolującą emalią w procesie powlekania zanurzeniowego. Proces powlekania drutu jest absolutnie niezbędny z następujących powodów:
- Aby zabezpieczyć uzwojenie przed absorpcją wilgoci
- Odporność na wstrząsy, wibracje i obciążenia mechaniczne poprzez mechaniczne połączenie całego uzwojenia, drutów i izolacji w jednolitą masę spoistą
- W celu ochrony uzwojenia przed niszczącym działaniem oleju, kwasu i innych chemikaliów, wilgoci, ciepła i pleśni oraz w celu zapewnienia właściwości zapobiegających śledzeniu
- Aby poprawić właściwości elektryczne izolatorów włóknistych lub innych, które powinny pozostawać nienaruszone przez którykolwiek z różnych wpływów destrukcyjnych przez pewien czas (na przykład - normalne cykle ciepła i zimna wynikające z włączania i wyłączania)
Najczęstsze emalie z drutu to: formal poliwinylowy, poliuretan (PUR), poliester, poliester do lutowania (PEI), poliamid-imid i poliimid, które zachowują się inaczej pod względem - przyczepności, elastyczności, szoku cieplnego, lutowności, gładkości i szybkości. Wybór rodzaju drutu emaliowanego zależy od wymagań konkretnego zastosowania.
Druty powlekane (znane również jako druty magnetyczne) są wytwarzane przez nałożenie powłoki emalii na włókno miedziane lub aluminiowe przewodnik w wielu warstwach. Przewodnik przepuszcza się przez płynną kąpiel szkliwa lub roztwór szkliwa w rozpuszczalniku, a następnie ogrzewa w piecu w celu usunięcia rozpuszczalnika i utwardzenia szkliwa; proces ten jest przeprowadzany kilkakrotnie kilkakrotnie w zależności od zastosowania.
Grubość powłoki, która zależy od procentowej zawartości części stałych w roztworze do powlekania, jest ważnym parametrem projektowym i bardzo ważne jest kontrolowanie jej w określonym z góry zakresie. Jeśli roztwór do powlekania zawiera wysoką zawartość procentową ciał stałych, koszty rozpuszczalnika można zmniejszyć. The grubość powłoki jest silnie zależny od lepkość ciekłego szkliwa lub roztworu szkliwa i lepkości roztworu szkliwa należy dokładnie kontrolować, aby uzyskać jednolita powłoka grubość. Gdy lepkość zmienia się poza specyfikacją, warstwa emaliowanego drutu będzie nierówna, co ostatecznie doprowadzi do złej jakości i często jest złomowane. Lepkość może mieć kilka skutków dla absorpcji, siły koloru i suszenia. Wysoce lepkie roztwory powłokowe powodują kleistość i powodują trudności w przenoszeniu na podłoże, natomiast niska lepkość sprawia, że jest bardziej mobilny i trudniejszy do kontrolowania, a także skutkuje zwiększonym zużyciem rozpuszczalnika. Lepkość wzrasta, gdy nie jest obrabiana, i maleje, gdy występuje stała siła przyłożona. Silna korelacja między temperaturą a lepkością atramentu sugeruje, że wahania temperatury mogą mieć drastyczny wpływ na lepkość, a tym samym grubość powłoki, która jest najważniejszym parametrem.
Aby uzyskać jednolitą powłokę i aby nie marnować emalii, jest zatem wysoce pożądane, aby lepkość emalii była automatycznie regulowana do zasadniczo stałej wartości. Monitorowanie lepkości w czasie rzeczywistymoring i kontrola procesu powlekania są niezbędne do poprawy wydajności i zmniejszenia kosztów w prawie każdym procesie powlekania drutu. Operatorzy procesów zdają sobie sprawę z potrzeby wiskozymetru monitorującego lepkość i temperaturę i mogą wykorzystywać lepkość z kompensacją temperatury jako kluczową zmienną procesową, aby zapewnić spójność i zmniejszyć odsetek odrzutów.
Dlaczego lepkość jest monitorowanaoring i kontrola mają kluczowe znaczenie w procesie powlekania drutu?
Szerokie i znaczące czynniki, które sprawiają, że zarządzanie lepkością ma kluczowe znaczenie w procesie powlekania drutu, to:
- Jakość powłoki: Przewody magnetyczne muszą być zgodne ze specyfikacjami gotowego produktu i wymogami regulacyjnymi, a kontrola procesu ma kluczowe znaczenie dla zapewnienia zgodności. Zmiana lepkości powoduje znaczną zmianę właściwości powłok rozpuszczalnikowych, a także wodnych, co wpływa na drukowność, odporność na blaknięcie i suszenie.
- Jednorodność powłoki: Inline monitor lepkościoring i kontrola mogą pomóc w osiągnięciu wymaganej jakości powłoki i ograniczeniu uszkodzeń powłoki, takich jak skórka pomarańczowa, odklejanie się i problemy z przyczepnością.
- Zmniejsz liczbę błędów powlekania: Kontrola lepkości może pomóc złagodzić częstotliwość błędów - przylepianie i zbieranie, bliźniactwo, obieranie, dzielenie, pękanie, szorstkość, powstawanie pęcherzy, mostkowanie i erozja powierzchni.
- Lepsza wydajność: Zapewnienie spójności w całym procesie powlekania znacznie zmniejsza wskaźniki odrzucania, oszczędzając koszty i czas. Techniki pomiaru offline są żmudne i niewiarygodne oraz wiążą się z dużymi opóźnieniami w procesie produkcyjnym, a ponadto wiążą się z wysokimi kosztami personelu przy próbkowaniu i przeprowadzaniu testów.
- Prawidłowe właściwości: Słaba jakość powłoki może niekorzystnie wpłynąć na pożądane właściwości drutów magnetycznych - hermetyczność i odporność na wypalenie, elastyczność, właściwości mechaniczne i chemiczne, zabarwienie i akceptację na rynku. Wszystkie te właściwości zależą od grubości i jednorodności powłoki, stąd krytyczne znaczenie ma kontrolowanie lepkości.
- Koszty: Powłoka o niewłaściwej lepkości szkodzi nie tylko jakości. Niewłaściwe zarządzanie lepkościami zwiększa zużycie pigmentów i rozpuszczalników, wpływając na marże.
- Marnotrawstwo: Materiały odrzucone z powodu złej jakości można zmniejszyć przy odpowiednim zarządzaniu lepkością.
- Wydajność: Wyeliminowanie ręcznej kontroli lepkości zwalnia czas operatorów i pozwala im skupić się na innych zadaniach.
- Przyjazna dla środowiska: Zmniejszenie zużycia pigmentu i rozpuszczalnika jest korzystne dla środowiska.
- Zgodność z przepisami: Globalne i krajowe przepisy określają ogólne właściwości elektryczne i mechaniczne drutów. Niezastosowanie się do tego ze względu na zmienność produkcji może prowadzić do znacznych szkód i strat klientów, oprócz zobowiązań wynikających z wadliwego wykonania w procesie produkcyjnym.
Aby zapewnić spójną, jednolitą powłokę o wysokiej jakości, zmiana lepkości w całym strumieniu procesowym jest monitorowana w czasie rzeczywistym, wykonując pomiary od linii podstawowej, a nie po prostu mierząc wartości bezwzględne, i dokonując korekt lepkości poprzez dostosowanie rozpuszczalników i kompensację temperatury do utrzymać cały proces powlekania w określonych granicach.
Wyzwania procesowe
Operatorzy na rynku powłok izolacyjnych dostrzegają potrzebę monitorowania lepkości, ale dokonywanie pomiarów poza laboratorium stanowiło wyzwanie dla inżynierów procesowych i działów jakości na przestrzeni lat. Istniejące wiskozymetry laboratoryjne mają niewielką wartość w środowiskach procesowych, ponieważ na lepkość ma bezpośredni wpływ temperatura, szybkość ścinania i inne zmienne, które są bardzo różne w off-line od tego, co są w linii. Konwencjonalne metody kontrolowania lepkości powłoki emaliowej okazały się nieodpowiednie nawet w zastosowaniach, w których dopuszczalna jest duża zmienność lepkości emalii, a powłoki druciane mogą różnić się od określonego z góry zakresu specyfikacji.
Tradycyjnie operatorzy mierzyli lepkość farby drukarskiej za pomocą kubka wypływowego. Próbka rozpuszczonego płynu z farby jest próbkowana w czasie za pomocą kubka dozującego, gdzie czas potrzebny na ból przechodzący przez lejek (kubek wypływowy) jest uważany za wskaźnik lepkości względnej. Procedura jest chaotyczna i czasochłonna, szczególnie jeśli atrament musi zostać najpierw przefiltrowany. Jest dość niedokładny, niespójny i niepowtarzalny nawet w przypadku doświadczonego operatora. Z powodu ciągłego procesu produkcji drutu emaliowanego próbkowanie interwałowe powoduje nadmierne opóźnienia. Lepkości rozpuszczonej cieczy w farbie nie można regulować w czasie rzeczywistym. Poza tym różne cylindry procesu cienkiej powłoki lakierniczej są otwarte; z powodu zmian temperatury otoczenia, wilgotności i innych czynników, takich jak temperatura, suchy klimat, rozpuszczalniki do farb mogą być lotne, ta technika pomiaru lepkości staje się nieskuteczna w odniesieniu do potrzeb procesu.
Niektóre firmy stosują systemy zarządzania temperaturą, aby utrzymać punkt aplikacji w określonej optymalnej temperaturze w celu uzyskania stałej lepkości. Ale temperatura nie jest jedynym czynnikiem wpływającym na lepkość. Szybkość ścinania, warunki przepływu, ciśnienie i inne zmienne mogą również wpływać na zmiany lepkości. Systemy z kontrolowaną temperaturą mają również długi czas instalacji i dużą powierzchnię.
Rheonics' Rozwiązania
Zautomatyzowany pomiar i kontrola lepkości w linii ma kluczowe znaczenie dla kontrolowania receptury powłoki i lepkości aplikacji. Rheonics oferuje następujące rozwiązania oparte na zrównoważonym rezonatorze skrętnym do kontroli i optymalizacji procesu powlekania:
- Coaching Lepkość pomiary: Rheonics" SRV jest szerokopasmowym, wbudowanym urządzeniem do pomiaru lepkości z wbudowanym pomiarem temperatury płynu i jest w stanie wykrywać zmiany lepkości w dowolnym strumieniu procesu w czasie rzeczywistym.
- Coaching Lepkość i gęstość pomiary: Rheonics" SRD jest liniowym przyrządem do pomiaru gęstości i lepkości z wbudowanym pomiarem temperatury płynu. Jeśli pomiar gęstości jest ważny dla twoich operacji, SRD jest najlepszym czujnikiem, który zaspokoi twoje potrzeby, z możliwościami operacyjnymi podobnymi do SRV wraz z dokładnymi pomiarami gęstości.
Zautomatyzowany pomiar lepkości online za pomocą SRV lub SRD eliminuje różnice w pobieraniu próbek i technikach laboratoryjnych stosowanych do pomiaru lepkości tradycyjnymi metodami. Czujnik jest instalowany w wiadrze z emaliowaną powłoką lub w linii, przez którą powłoka jest pompowana do aplikatora, stale mierząc lepkość sformułowanego systemu (i gęstość w przypadku SRD). Spójność powłoki osiąga się poprzez automatyzację systemu dozowania za pomocą kontrolera procesu opartego na pomiarach lepkości i temperatury w czasie rzeczywistym. Zastosowanie SRV na linii technologicznej powlekania poprawia wydajność transferu powłoki, poprawiając wydajność, marże zysku i cele środowiskowe / regulacyjne. Czujniki mają kompaktową obudowę, co ułatwia instalację OEM i modernizację. Nie wymagają konserwacji ani ponownej konfiguracji. Czujniki zapewniają dokładne, powtarzalne wyniki bez względu na to, jak i gdzie są zamontowane, bez potrzeby stosowania specjalnych komór, gumowych uszczelek lub ochrony mechanicznej. Bez użycia materiałów eksploatacyjnych, SRV i SRD są niezwykle łatwe w obsłudze przy zerowej konserwacji.
Rheonics' Korzyść
Kompaktowy kształt, brak ruchomych części i zerowa konserwacja
Rheonics' SRV i SRD mają bardzo małe wymiary, co ułatwia instalację OEM i modernizację. Umożliwiają łatwą integrację z dowolnym strumieniem procesu. Są łatwe w czyszczeniu i nie wymagają konserwacji ani ponownej konfiguracji. Ich niewielka powierzchnia umożliwia prostą instalację w linii, bez konieczności stosowania dodatkowej przestrzeni lub adaptera na powlekarce.
Wysoka stabilność i niewrażliwość na warunki montażu: Możliwa dowolna konfiguracja
Rheonics SRV i SRD wykorzystują unikalny, opatentowany rezonator współosiowy, w którym dwa końce czujników skręcają się w przeciwnych kierunkach, eliminując momenty reakcji podczas ich montażu, a tym samym czyniąc je całkowicie niewrażliwymi na warunki montażu i natężenie przepływu atramentu. Czujniki te z łatwością radzą sobie z regularną przeprowadzką. Element czujnika znajduje się bezpośrednio w płynie, bez konieczności stosowania specjalnej obudowy lub klatki ochronnej.
Natychmiastowe dokładne odczyty warunków drukowania - Pełny przegląd systemu i sterowanie predykcyjne
RheonicsOprogramowanie jest potężne, intuicyjne i wygodne w obsłudze. Lepkość można monitorować w czasie rzeczywistym na komputerze. Za pomocą jednego pulpitu nawigacyjnego zarządza się wieloma czujnikami rozmieszczonymi w całej fabryce. Pulsacja ciśnienia spowodowana pompowaniem nie ma wpływu na działanie czujnika ani dokładność pomiaru. Ponadto czujnik jest niewrażliwy na wibracje i zakłócenia elektryczne pochodzące z urządzeń zewnętrznych.
Łatwa instalacja i brak konieczności ponownej konfiguracji / ponownej kalibracji
Wymień czujniki bez wymiany lub przeprogramowywania elektroniki
Zamontowane zamienniki dla czujnika i elektroniki bez aktualizacji oprogramowania lub zmian współczynnika kalibracji.
Łatwy montaż. Wkręca się w złączki gwintowane ¾ ”NPT lub połączenia kołnierzowe.
Żadnych komór, O-ring uszczelki lub uszczelki.
Łatwo zdejmowany do czyszczenia lub kontroli.
SRV dostępny z kołnierzem, DIN 11851 higieniczny i tri-clamp złącze ułatwiające montaż i demontaż.
Niskie zużycie energii
Zasilacz 24 V DC o poborze prądu mniejszym niż 0.1 A podczas normalnej pracy (mniej niż 3 W)
Krótki czas reakcji i lepkość kompensowana temperaturą
Ultraszybka i solidna elektronika w połączeniu z kompleksowymi modelami obliczeniowymi sprawia, że Rheonics urządzenia jedne z najszybszych i najdokładniejszych w branży. SRV i SRD umożliwiają dokładne pomiary lepkości (i gęstości w przypadku SRD) w czasie rzeczywistym co sekundę i nie mają na nie wpływu zmiany natężenia przepływu!
Szerokie możliwości operacyjne
RheonicsPrzyrządy są zbudowane tak, aby wykonywać pomiary w najtrudniejszych warunkach. SRV ma najszerszy zakres operacyjny na rynku wiskozymetrów procesowych inline:
- Zakres ciśnienia do 5000 psi i więcej
- Zakres temperatur od -40 do 300 ° C
- Zakres lepkości: 0.5 cP do 50,000 XNUMX+ cP
SRD: Pojedynczy instrument, potrójna funkcja - Lepkość, temperatura i gęstość
Rheonics" SRD to wyjątkowy produkt, który zastępuje trzy różne przyrządy do pomiaru lepkości, gęstości i temperatury. Eliminuje trudności związane ze wspólną lokalizacją trzech różnych instrumentów i zapewnia niezwykle dokładne i powtarzalne pomiary w najtrudniejszych warunkach.
Osiągnij odpowiednią jakość powłoki, obniż koszty i zwiększ produktywność
Zintegruj SRV lub SRD z linią procesową i zapewnij jednorodność i spójność w całym procesie powlekania. Uzyskaj stałe kolory i grubość bez martwienia się o różnice w kolorze lub grubości. SRV (i SRD) stale monitoruje i kontroluje lepkość (i gęstość w przypadku SRD) i zapobiega nadużywaniu drogich pigmentów i rozpuszczalników. Niezawodne i automatyczne podawanie atramentu zapewnia szybszą pracę maszyn i oszczędza czas operatorów. Zoptymalizuj proces powlekania za pomocą SRV i uzyskaj mniej odrzutów, mniej odpadów, mniej reklamacji klientów, mniej przestojów pras i oszczędność kosztów materiałów. A na koniec przyczynia się do lepszych wyników finansowych i lepszego środowiska!
Czyszczenie na miejscu (CIP)
SRV (i SRD) monitoruje czyszczenie linii atramentu przez monitoring lepkość (i gęstość) rozpuszczalnika podczas fazy czyszczenia. Czujnik wykrywa wszelkie drobne pozostałości, umożliwiając operatorowi podjęcie decyzji, kiedy linia jest celowo czysta. Alternatywnie SRV dostarcza informacje do automatycznego systemu czyszczenia, aby zapewnić pełne i powtarzalne czyszczenie pomiędzy cyklami.
Doskonała konstrukcja i technologia czujnika
Zaawansowana, opatentowana elektronika trzeciej generacji steruje tymi czujnikami i ocenia ich reakcję. SRV i SRD są dostępne ze standardowymi przyłączami procesowymi, takimi jak ¾” NPT i 3” Tri-clamp umożliwiając operatorom wymianę istniejącego czujnika temperatury w linii technologicznej na SRV/SRD, dostarczając bardzo cennych i przydatnych informacji o płynie procesowym, takich jak lepkość, oprócz dokładnego pomiaru temperatury za pomocą wbudowanego czujnika Pt1000 (dostępna klasa AA, A, B DIN EN 60751) .
Przyjazna dla środowiska
Ogranicz zużycie LZO (lotnych związków organicznych) w procesie, zmniejszając energię potrzebną do jego odzyskania lub koszty utylizacji. Wytwarzaj inteligentnie, jednocześnie oszczędzając koszty, zapewniając wysoką jakość i chroniąc środowisko.
Elektronika zbudowana tak, aby pasowała do Twoich potrzeb
Dostępne w obudowie przetwornika w wykonaniu przeciwwybuchowym i niewielkim obudowie na szynę DIN, elektronika czujnika umożliwia łatwą integrację z rurociągami procesowymi i wewnątrz szaf urządzeń.
Łatwa integracja
Wiele analogowych i cyfrowych metod komunikacji zaimplementowanych w elektronice czujnika sprawia, że podłączenie do przemysłowych sterowników PLC i systemów sterowania jest proste i proste.
Zgodność z ATEX i IECEx
Rheonics oferuje czujniki iskrobezpieczne z certyfikatami ATEX i IECEx do stosowania w środowiskach niebezpiecznych. Czujniki te spełniają zasadnicze wymagania bezpieczeństwa i higieny pracy związane z projektowaniem i konstrukcją urządzeń i systemów ochronnych przeznaczonych do stosowania w przestrzeniach zagrożonych wybuchem.
Posiadane przez firmę certyfikaty iskrobezpieczności i przeciwwybuchowości Rheonics pozwala także na dostosowanie istniejącego czujnika, pozwalając naszym klientom uniknąć czasu i kosztów związanych z identyfikacją i testowaniem alternatywy. Można dostarczyć czujniki niestandardowe do zastosowań wymagających od jednej jednostki do tysięcy jednostek; z czasem realizacji wynoszącym tygodnie zamiast miesięcy.
Rheonics SRV & SRD posiadają zarówno certyfikat ATEX, jak i IECEx.
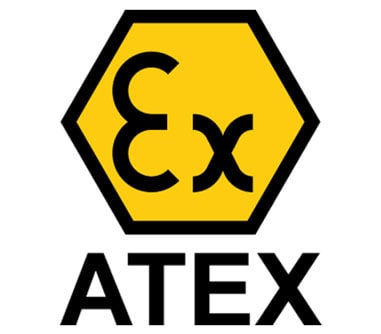
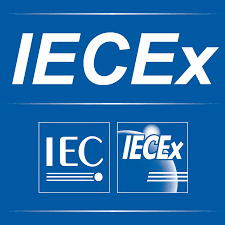
Realizacja
Zainstaluj czujnik bezpośrednio w strumieniu procesowym, aby wykonywać pomiary lepkości i gęstości w czasie rzeczywistym. Nie jest wymagany przewód obejściowy: czujnik można zanurzyć bezpośrednio w strumieniu procesowym. Natężenie przepływu powłoki i wibracje maszyny nie wpływają na stabilność i dokładność pomiaru. Rheonics czujniki i rozwiązania do kontroli powłok pomagają zoptymalizować wydajność powłok, zapewniając powtarzalne, kolejne i spójne wyniki rok po roku.
Rheonics Wybór instrumentu
Rheonics projektuje, produkuje i sprzedaje innowacyjne czujniki i monitory płynóworing systemy. Precyzja zbudowana w Szwajcarii, RheonicsWiskozymetry i gęstościomierze in-line charakteryzują się czułością wymaganą w danym zastosowaniu i niezawodnością niezbędną do przetrwania w trudnych warunkach operacyjnych. Stabilne wyniki – nawet w niekorzystnych warunkach przepływu. Brak wpływu spadku ciśnienia lub natężenia przepływu. Równie dobrze nadaje się do pomiarów kontroli jakości w laboratorium. Nie ma potrzeby zmiany żadnego komponentu ani parametru, aby mierzyć w pełnym zakresie.
Sugerowane produkty do zastosowania
- Szeroki zakres lepkości - monitoruj cały proces
- Powtarzalne pomiary zarówno płynów newtonowskich, jak i nienewtonowskich, płynów jednofazowych i wielofazowych
- Hermetycznie zamknięte, wszystkie części ze stali nierdzewnej 316L zwilżane
- Wbudowany pomiar temperatury płynu
- Kompaktowy kształt ułatwiający instalację w istniejących liniach technologicznych
- Łatwy w czyszczeniu, nie wymaga konserwacji ani ponownej konfiguracji
- Pojedynczy przyrząd do pomiaru gęstości procesowej, lepkości i temperatury
- Powtarzalne pomiary zarówno płynów newtonowskich, jak i nienewtonowskich, płynów jednofazowych i wielofazowych
- Konstrukcja wykonana w całości z metalu (stal nierdzewna 316L)
- Wbudowany pomiar temperatury płynu
- Kompaktowy kształt ułatwiający montaż w istniejących rurach
- Łatwy w czyszczeniu, nie wymaga konserwacji ani ponownej konfiguracji