Wprowadzenie
Powlekanie błoną stałych doustnych postaci dawkowania jest dobrze ugruntowanym procesem w przemyśle farmaceutycznym. Większość postaci dawkowania tabletek przechodzi proces powlekania błoną. Głównym celem powlekania postaci dawkowania w postaci filmu o natychmiastowym uwalnianiu jest zapewnienie identyfikacji koloru, zwiększenie stabilności i maskowanie smaku. Dodatkowo ułatwia przetwarzanie i obsługę podczas produkcji farmaceutycznej, dzięki czemu jest szeroko stosowany w przemyśle farmaceutycznym. Wiele stałych farmaceutycznych postaci dawkowania jest wytwarzanych z powłokami, albo na zewnętrznej powierzchni tabletki, albo na materiałach dozowanych w żelatynowych kapsułkach. Proces powlekania można specjalnie opracować, aby regulować szybkość rozpuszczania tabletki i miejsce wchłaniania aktywnych leków do organizmu po spożyciu. Istnieją różne rodzaje urządzeń do powlekania tabletek (standardowa miska do powlekania, perforowana miska do powlekania, powlekanie ze złożem fluidalnym) i techniki (powlekanie cukrem, powlekanie filmem i powlekanie jelitowe) - zasada działania, projekt, struktura, pojemność powietrza, skład powłoki i wydajność określają wybór.
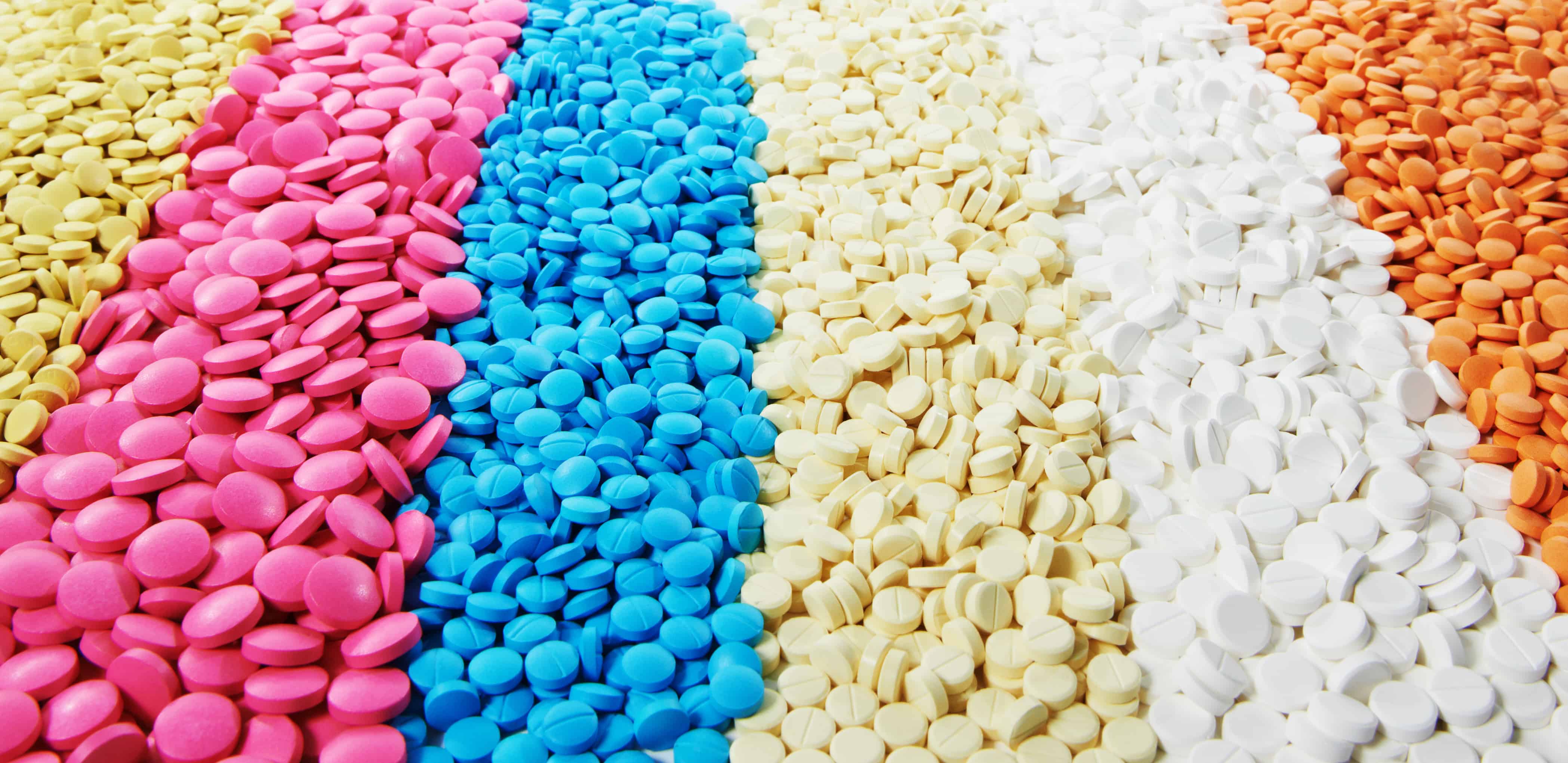
Zastosowanie
Z biegiem czasu procesy powlekania rozwinęły się ze sztuki z wcześniejszych lat do tych, które są bardziej zaawansowane technologicznie i kontrolowane, tak aby ułatwić przestrzeganie dobrych praktyk wytwarzania (GMP). Formuła powłoki i optymalizacja procesu przy użyciu metod naukowych przeważyły nad tradycyjnymi metodami powlekania błoną. Proces powlekania błoną polega na konsekwentnym nanoszeniu i suszeniu jednolitego preparatu powlekającego na powierzchnię podłoża, aby utworzyć jednorodną błonę. Kontrola parametrów procesu jest niezwykle ważna dla dobrego powlekania tabletek.
3 podstawowe składniki związane z powlekaniem tabletek to właściwości tabletek, proces powlekania i skład powłoki. Wynik procesu powlekania jest silnie zależny od właściwości reologicznych zastosowanej dyspersji powłoki filmowej. Zagadnienia takie jak pomostowanie logo, skórka pomarańczowa i suszenie rozpryskowe mają swoje korzenie w lepkich i elastycznych właściwościach powłoki. Określenie i ocena właściwości reologicznych ma zatem ogromne znaczenie dla uniknięcia problemów podczas procesu powlekania błoną.
Ponadto w dziedzinie powlekania błoną błyskawicznego uwalniania czas procesu, a w rezultacie koszty wytwarzania, są bezpośrednio związane z zawartością substancji stałej w dyspersji. Ponieważ lepkość jest specyficzną cechą polimeru błonotwórczego, badanie reologiczne jest bardzo przydatne i ważne w celu wybrania najbardziej ekonomicznego preparatu. Polimery rozpuszczalne w wodzie stosuje się głównie do powlekania błoną o natychmiastowym uwalnianiu (IR). Te substancje tworzące film są rozprowadzane w postaci proszku. Podczas przygotowywania formulacji powłoki filmowej polimery rozpuszcza się w wodzie. Pomimo tego, że polimery te można stosować do powłok chroniących przed wilgocią, nie uzyskuje się przez nie pewnych funkcji. Jednak rozpuszczanie polimerów w wodzie może powodować znaczącą zmianę właściwości płynnych ciekłego nośnika. Wzrost lepkości i zmiany napięcia powierzchniowego wpływają na tworzenie kropel podczas natryskiwania, a także tworzenie filmu, a zatem na jakość powierzchni powlekanych rdzeni. Typowe dyspersje powłok filmowych IR składają się z różnych zaróbek - co najmniej jeden lub kombinacja różnych polimerów błonotwórczych, pigmentów i opcjonalnych plastyfikatorów jest potrzebny do utworzenia kolorowej folii na powierzchni rdzenia. Biorąc pod uwagę listę substancji pomocniczych w preparacie powłokowym, polimer błonotwórczy jest jedynym materiałem powodującym znaczną zmianę lepkości i właściwości płynięcia dyspersji powłokowej w dużym stopniu wpływającym na wynik powlekania.
Ogólnie można założyć, że przy niższej lepkości:
- Przygotowanie dyspersji powłoki jest szybsze
- Ryzyko tworzenia się grudek jest niższe
- Jakość powierzchni tabletek powlekanych jest lepsza
- Maksymalna zawartość substancji stałych w dyspersji jest wyższa
- Czas przetwarzania jest krótszy
- Koszty przetwarzania są niższe
Każdy preparat do powlekania i polimer błonotwórczy ma swoją charakterystyczną granicę maksymalnej wartości lepkości dla przetwarzalności, która zależy od wielkości partii, wyposażenia do powlekania i procesu. Aby zoptymalizować wydajność i jakość, absolutnie konieczne jest zrekompensowanie utraty rozpuszczalnika przez dodanie od czasu do czasu niewielkiej ilości rozcieńczalnika, aby zachować optymalną lepkość do użycia. Elementy sterujące umożliwiają koordynację działania wszystkich komponentów w celu osiągnięcia pożądanych rezultatów.
Dlaczego zarządzanie lepkością ma kluczowe znaczenie w procesie drukowania w farmacji?
Szerokie i znaczące czynniki, które sprawiają, że zarządzanie lepkością ma kluczowe znaczenie w druku farmaceutycznym to:
- Jakość powłoki: Tablety muszą być zgodne ze specyfikacjami gotowego produktu i wszelkimi odpowiednimi wymogami uzupełniającymi, co można zapewnić. Zmiana lepkości powoduje znaczącą zmianę właściwości atramentu zarówno rozpuszczalnikowego, jak i wodnego, co wpływa na drukowność, odporność na blaknięcie i schnięcie.
- Zmniejsz liczbę błędów powlekania: Kontrola lepkości może pomóc złagodzić częstotliwość błędów - przylepianie i zbieranie, bliźniactwo, obieranie, dzielenie, pękanie, szorstkość, powstawanie pęcherzy, mostkowanie i erozja powierzchni.
- Kolor: Spójność kolorów i gęstość kolorów mają decydujące znaczenie dla właściwej jakości druku. Kontrolowanie lepkości atramentu jest kluczem do spójności kolorów, ponieważ jest to czynnik podlegający największej zmienności. Procentowa zawartość części stałych w płynie jest cechą tuszu, który nadaje mu kolor. Lepkość tuszu jest wskaźnikiem procentowym zawartości części stałych w płynie.
- Koszty: Drukowanie z niewłaściwą lepkością szkodzi nie tylko jakości. Niewłaściwe zarządzanie lepkościami zwiększa zużycie pigmentów i rozpuszczalników, wpływając na marże.
- Marnotrawstwo: Materiały odrzucone z powodu złej jakości można zmniejszyć przy odpowiednim zarządzaniu lepkością.
- Wydajność: Wyeliminowanie ręcznej kontroli lepkości zwalnia czas operatorów i pozwala im skupić się na innych zadaniach.
- Środowisko: Zmniejszenie zużycia pigmentu i rozpuszczalnika jest korzystne dla środowiska.
- Weryfikacja: Identyfikacja dawki pomaga w różnicowaniu produktu i zwiększa bezpieczeństwo produktu. Być może w większym stopniu niż inne branże, powłoki farmaceutyczne wymagają najwyższej jakości druku. Czytelność i kontrast nie podlegają negocjacjom, jeśli chodzi o kody regulacyjne i identyfikowalność.
Aby zapewnić spójne drukowanie w wysokiej jakości, zmiana lepkości atramentu w całym strumieniu procesowym jest monitorowana w czasie rzeczywistym, wykonując pomiary od linii podstawowej, a nie po prostu mierząc wartości bezwzględne, oraz dostosowując lepkość, dostosowując rozpuszczalniki i temperaturę, aby utrzymać ją w granicach określone limity.
Wyzwania procesowe
Ponieważ natryskiwanie, rozprowadzanie powłoki i suszenie zachodzą w tym samym czasie, powlekanie tabletek jest dynamicznym, złożonym procesem, na który wpływa wiele zmiennych. Aby zoptymalizować wydajność i jakość, absolutnie konieczne jest skompensowanie utraty rozpuszczalnika poprzez dodanie od czasu do czasu niewielkiej ilości rozcieńczalnika podczas operacji, aby utrzymać optymalną lepkość do użycia poprzez regulacje zgodnie z warunkami.
Istniejące wiskozymetry laboratoryjne mają niewielką wartość w środowiskach procesowych, ponieważ na lepkość ma bezpośredni wpływ temperatura, szybkość ścinania i inne zmienne, które są bardzo różne w off-line od tego, co są w linii. Tradycyjnie operatorzy mierzyli lepkość farby drukarskiej za pomocą kubka wypływowego. Procedura jest chaotyczna i czasochłonna, szczególnie jeśli atrament musi zostać najpierw przefiltrowany. Jest dość niedokładny, niespójny i niepowtarzalny nawet w przypadku doświadczonego operatora.
Niektóre firmy stosują systemy zarządzania temperaturą, aby utrzymać punkt aplikacji w określonej optymalnej temperaturze w celu uzyskania stałej lepkości atramentu. Ale temperatura nie jest jedynym czynnikiem wpływającym na lepkość. Szybkość ścinania, warunki przepływu, ciśnienie i inne zmienne mogą również wpływać na zmiany lepkości. Systemy z kontrolowaną temperaturą mają również długi czas instalacji i dużą powierzchnię.
Konwencjonalne wiskozymetry wibracyjne są niezrównoważone i wymagają dużych mas, aby uniknąć dużego wpływu sił montażowych.
Rheonics' Rozwiązania
Zautomatyzowany pomiar i kontrola lepkości w linii ma kluczowe znaczenie dla kontrolowania lepkości atramentu. Rheonics oferuje następujące rozwiązania oparte na zrównoważonym rezonatorze skrętnym do kontroli i optymalizacji procesu drukowania:
- In-line Lepkość pomiary: Rheonics" SRV jest szerokopasmowym, wbudowanym urządzeniem do pomiaru lepkości z wbudowanym pomiarem temperatury płynu i jest w stanie wykrywać zmiany lepkości w dowolnym strumieniu procesu w czasie rzeczywistym.
- In-line Lepkość i gęstość pomiary: Rheonics" SRD jest równoległym przyrządem do pomiaru gęstości i lepkości z wbudowanym pomiarem temperatury płynu. Jeśli pomiar gęstości jest ważny dla twoich operacji, SRD jest najlepszym czujnikiem, który zaspokoi twoje potrzeby, z możliwościami operacyjnymi podobnymi do SRV wraz z dokładnymi pomiarami gęstości.
Zautomatyzowany pomiar lepkości w linii za pomocą SRV lub SRD eliminuje różnice w pobieraniu próbek i technikach laboratoryjnych, które są stosowane do pomiaru lepkości tradycyjnymi metodami. Czujnik jest umieszczony w linii, dzięki czemu stale mierzy lepkość atramentu (i gęstość w przypadku SRD). Spójność drukowania osiąga się poprzez automatyzację systemu dozowania za pomocą sterownika wykorzystującego ciągłe pomiary lepkości w czasie rzeczywistym. Zastosowanie SRV na linii procesu drukowania poprawia wydajność transferu atramentu, poprawiając wydajność, marże zysku i cele środowiskowe. Oba czujniki mają kompaktową obudowę, co ułatwia instalację OEM i modernizację. Nie wymagają konserwacji ani ponownej konfiguracji. Oba czujniki oferują dokładne, powtarzalne wyniki bez względu na to, jak i gdzie są zamontowane, bez potrzeby stosowania specjalnych komór, gumowych uszczelek lub ochrony mechanicznej. Bez użycia materiałów eksploatacyjnych, SRV i SRD są niezwykle łatwe w obsłudze.
Kompaktowy kształt, brak ruchomych części i nie wymaga konserwacji
Rheonics' SRV i SRD mają bardzo małe wymiary, co ułatwia instalację OEM i modernizację. Umożliwiają łatwą integrację z dowolnym strumieniem procesu. Są łatwe w czyszczeniu i nie wymagają konserwacji ani ponownej konfiguracji. Mają niewielką powierzchnię, co umożliwia instalację Inline w liniach atramentowych, co pozwala uniknąć dodatkowej przestrzeni lub wymagań dotyczących adapterów w prasie i wózkach z atramentem.
Wysoka stabilność i niewrażliwość na warunki montażu: Możliwa dowolna konfiguracja
Rheonics SRV i SRD wykorzystują unikalny, opatentowany rezonator współosiowy, w którym dwa końce czujników skręcają się w przeciwnych kierunkach, eliminując momenty reakcji podczas ich montażu, a tym samym czyniąc je całkowicie niewrażliwymi na warunki montażu i natężenie przepływu atramentu. Czujniki te z łatwością radzą sobie z regularną przeprowadzką. Element czujnika znajduje się bezpośrednio w płynie, bez konieczności stosowania specjalnej obudowy lub klatki ochronnej.
Natychmiastowe dokładne odczyty warunków drukowania - Pełny przegląd systemu i sterowanie predykcyjne
RheonicsOprogramowanie jest potężne, intuicyjne i wygodne w użyciu. Lepkość atramentu można monitorować na komputerze w czasie rzeczywistym. Zarządzanie wieloma czujnikami odbywa się z jednego pulpitu nawigacyjnego rozmieszczonego po całej hali produkcyjnej. Brak wpływu pulsacji ciśnienia podczas pompowania na działanie czujnika i dokładność pomiaru. Brak efektu wibracji prasy drukarskiej.
Łatwa instalacja i brak konieczności ponownej konfiguracji / ponownej kalibracji
Wymień czujniki bez wymiany lub przeprogramowania elektroniki, doraźne wymiany zarówno czujnika, jak i elektroniki, bez aktualizacji oprogramowania sprzętowego lub zmian współczynnika kalibracji. Łatwy montaż. Wkręca się w gwint ¾” NPT w złączce przewodu atramentowego. Żadnych komór, O-ring uszczelki lub uszczelki. Łatwe do usunięcia w celu czyszczenia lub kontroli. SRV dostępny z kołnierzem i tri-clamp złącze ułatwiające montaż i demontaż.
Niskie zużycie energii
Zasilacz 24 V DC o poborze prądu mniejszym niż 0.1 A podczas normalnej pracy
Krótki czas reakcji i lepkość kompensowana temperaturą
Ultraszybka i solidna elektronika w połączeniu z kompleksowymi modelami obliczeniowymi sprawia, że Rheonics urządzenia jedne z najszybszych i najdokładniejszych w branży. SRV i SRD umożliwiają dokładne pomiary lepkości (i gęstości w przypadku SRD) w czasie rzeczywistym co sekundę i nie mają na nie wpływu zmiany natężenia przepływu!
Szerokie możliwości operacyjne
RheonicsPrzyrządy są zbudowane tak, aby wykonywać pomiary w najtrudniejszych warunkach. SRV ma najszerszy zakres operacyjny na rynku wiskozymetrów procesowych inline:
- Zakres ciśnienia do 5000 psi
- Zakres temperatur od -40 do 200 ° C
- Zakres lepkości: 0.5 cP do 50,000 XNUMX cP
SRD: Pojedynczy instrument, potrójna funkcja - Lepkość, temperatura i gęstość
Rheonics' SRD to unikalny produkt, który zastępuje trzy różne przyrządy do pomiarów lepkości, gęstości i temperatury. Eliminuje trudności związane ze zlokalizowaniem trzech różnych instrumentów i zapewnia niezwykle dokładne i powtarzalne pomiary w najtrudniejszych warunkach.
Uzyskaj odpowiednią jakość druku, obniż koszty i zwiększ produktywność
Zintegruj SRV / SRD z linią technologiczną i zapewnij spójność kolorów podczas całego procesu drukowania. Osiągaj stałe kolory bez obawy o różnice kolorystyczne. SRV (i SRD) stale monitoruje i kontroluje lepkość (i gęstość w przypadku SRD) i zapobiega nadmiernemu zużyciu drogich pigmentów i rozpuszczalników. Niezawodne i automatyczne podawanie atramentu zapewnia, że prasy pracują szybciej i oszczędzają czas operatora. Zoptymalizuj proces drukowania za pomocą SRV i doświadcz mniejszej liczby odrzutów, mniej odpadów, mniej skarg klientów, mniej przestojów w prasie i oszczędność kosztów materiałów. A na koniec przyczynia się do lepszego wyniku i lepszego środowiska!
Czyszczenie na miejscu (CIP)
SRV (i SRD) monitoruje czyszczenie linii atramentu przez monitoring lepkość (i gęstość) rozpuszczalnika podczas fazy czyszczenia. Czujnik wykrywa wszelkie drobne pozostałości, umożliwiając operatorowi podjęcie decyzji, kiedy linia jest celowo czysta. Alternatywnie SRV (i SRD) dostarcza informacje do zautomatyzowanego systemu czyszczenia, aby zapewnić pełne i powtarzalne czyszczenie pomiędzy seriami, zapewniając w ten sposób pełną zgodność z normami sanitarnymi zakładów produkujących leki.
Doskonała konstrukcja i technologia czujnika
Zaawansowana, opatentowana elektronika trzeciej generacji steruje tymi czujnikami i ocenia ich reakcję. SRV i SRD są dostępne ze standardowymi przyłączami procesowymi, takimi jak ¾” NPT i 3” Tri-clamp umożliwiając operatorom wymianę istniejącego czujnika temperatury w linii technologicznej na SRV/SRD, dostarczając bardzo cennych i przydatnych informacji o płynie procesowym, takich jak lepkość, oprócz dokładnego pomiaru temperatury za pomocą wbudowanego czujnika Pt1000 (dostępna klasa AA, A, B DIN EN 60751) .
Elektronika zbudowana tak, aby pasowała do Twoich potrzeb
Dostępne w obudowie przetwornika w wykonaniu przeciwwybuchowym i niewielkim obudowie na szynę DIN, elektronika czujnika umożliwia łatwą integrację z rurociągami procesowymi i wewnątrz szaf urządzeń.
Łatwa integracja
Wiele analogowych i cyfrowych metod komunikacji zaimplementowanych w elektronice czujnika sprawia, że podłączenie do przemysłowych sterowników PLC i systemów sterowania jest proste i proste.
Realizacja
Zainstaluj czujnik bezpośrednio w strumieniu procesowym, aby wykonywać pomiary lepkości i gęstości w czasie rzeczywistym. Nie jest wymagana linia obejściowa: czujnik można zanurzyć w linii, szybkość przepływu i wibracje nie wpływają na stabilność i dokładność pomiaru. Zoptymalizuj proces decyzyjny, zapewniając powtarzalne, kolejne i spójne testy płynu.
Rheonics Wybór instrumentu
Rheonics projektuje, produkuje i sprzedaje innowacyjne czujniki i monitory płynóworing systemy. Precyzja zbudowana w Szwajcarii, RheonicsWiskozymetry in-line charakteryzują się czułością wymaganą w danym zastosowaniu i niezawodnością niezbędną do przetrwania w trudnych warunkach pracy. Stabilne wyniki – nawet w niekorzystnych warunkach przepływu. Brak wpływu spadku ciśnienia lub natężenia przepływu. Równie dobrze nadaje się do pomiarów kontroli jakości w laboratorium.
Sugerowane produkty do zastosowania
• Szeroki zakres lepkości - monitoruj cały proces
• Powtarzalne pomiary zarówno płynów newtonowskich, jak i nienewtonowskich, płynów jednofazowych i wielofazowych
• Konstrukcja wykonana w całości z metalu (stal nierdzewna 316L)
• Wbudowany pomiar temperatury płynu
• Kompaktowy kształt dla łatwej instalacji w istniejących liniach technologicznych
• Łatwy w czyszczeniu, nie wymaga konserwacji ani ponownej konfiguracji
• Pojedynczy przyrząd do pomiaru gęstości procesu, lepkości i temperatury
• Powtarzalne pomiary zarówno płynów newtonowskich, jak i nienewtonowskich, płynów jednofazowych i wielofazowych
• Konstrukcja wykonana w całości z metalu (stal nierdzewna 316L)
• Wbudowany pomiar temperatury płynu
• Kompaktowy kształt ułatwiający montaż w istniejących rurach
• Łatwy w czyszczeniu, nie wymaga konserwacji ani ponownej konfiguracji